Attention! Your ePaper is waiting for publication!
By publishing your document, the content will be optimally indexed by Google via AI and sorted into the right category for over 500 million ePaper readers on YUMPU.
This will ensure high visibility and many readers!
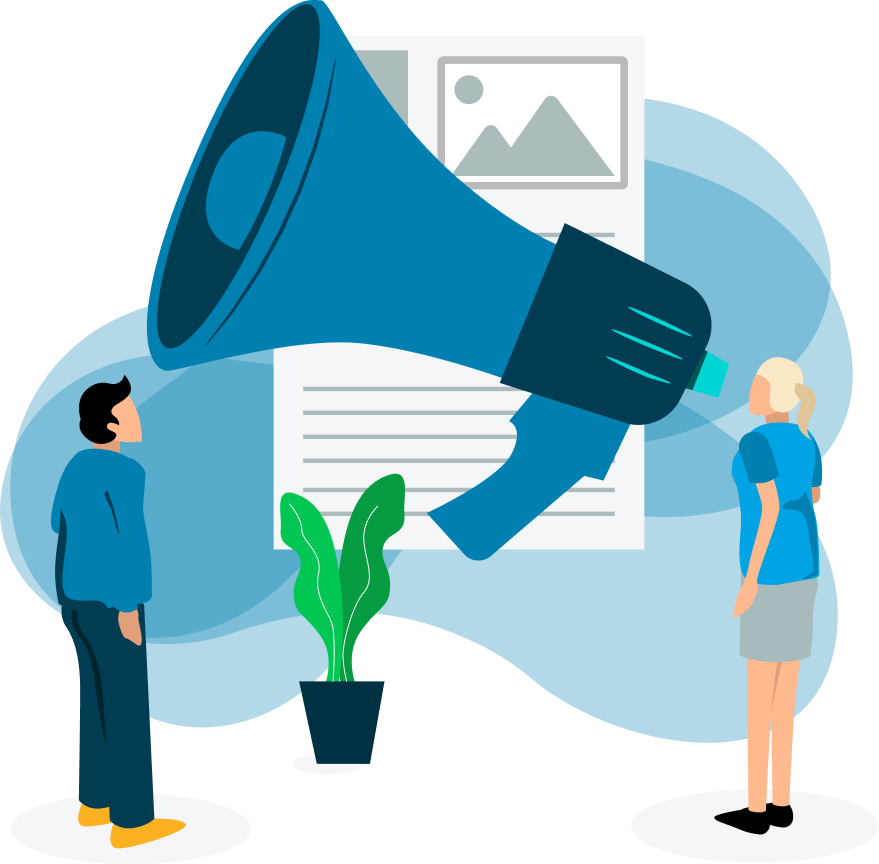
Your ePaper is now published and live on YUMPU!
You can find your publication here:
Share your interactive ePaper on all platforms and on your website with our embed function
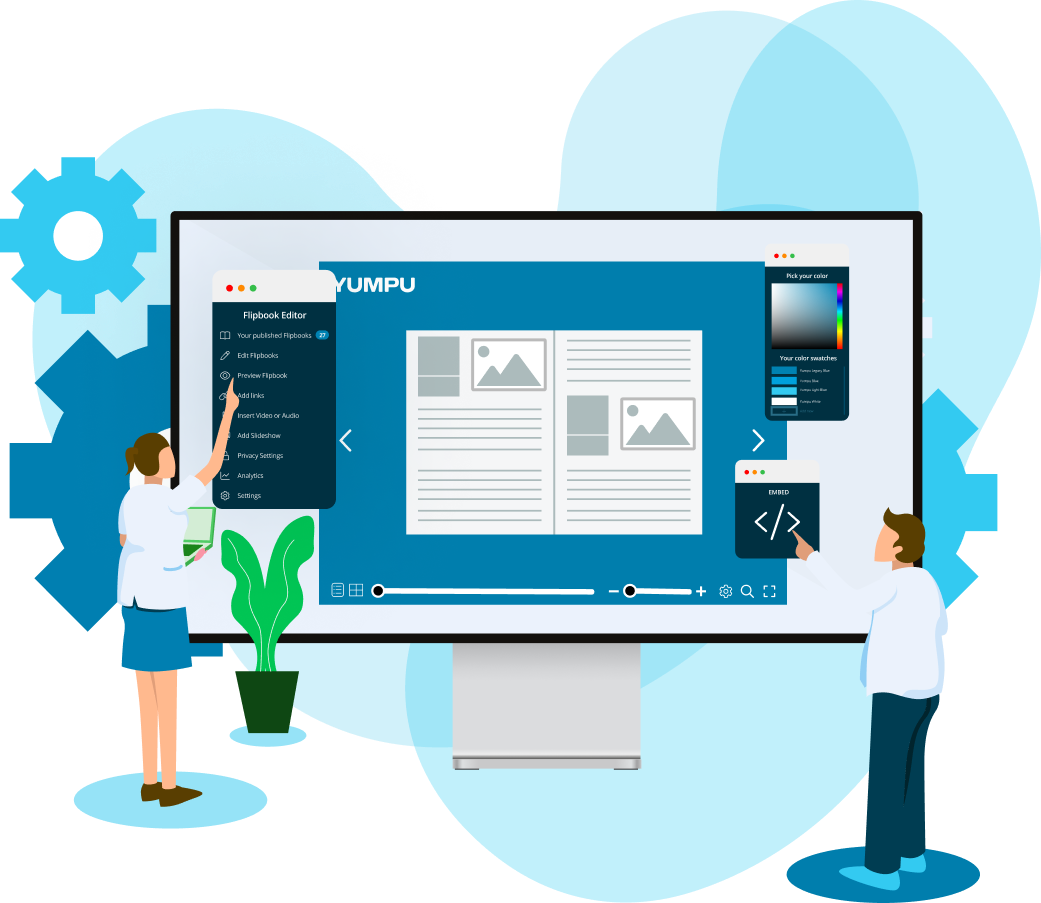
Handbook of Solvents - George Wypych - ChemTech - Ventech!
Handbook of Solvents - George Wypych - ChemTech - Ventech!
Handbook of Solvents - George Wypych - ChemTech - Ventech!
Create successful ePaper yourself
Turn your PDF publications into a flip-book with our unique Google optimized e-Paper software.
14.22 Polymers and man-made fibers 1017<br />
Figure 14.22.1. Schematic diagram <strong>of</strong> emissions from the polymer manufacturing industry. [Reproduced from<br />
EPA Office <strong>of</strong> Compliance Sector Notebook Project. Pr<strong>of</strong>ile <strong>of</strong> the Petroleum Refining Industry. US<br />
Environmental Protection Agency, 1995.]<br />
vent), and residual water and solvent are purged during polymer drying. Residual solvents<br />
are removed by further drying and extrusion. <strong>Solvents</strong> are also used in equipment cleaning.<br />
<strong>Solvents</strong> are <strong>of</strong>ten stored under a nitrogen blanket to minimize oxidation and contamination.<br />
When these systems are vented solvent losses occur. Figure 14.22.1 shows a schematic<br />
diagram <strong>of</strong> potential emissions during polymer manufacture.<br />
Manufacture <strong>of</strong> man-made fibers involves polymerization (usually the core part <strong>of</strong> the<br />
process), preparation <strong>of</strong> the solution, spinning, washing and coagulation, drying and other<br />
operations. Fibers are formed by forcing the viscous liquid through small-bore orifices. A<br />
suitable viscosity can be achieved either by heating or dissolution. The rheological properties<br />
<strong>of</strong> the solution are governed to a large degree by the solvents selected. Wastes generated<br />
during the spinning operation include evaporated solvent and wastewater contaminated by<br />
solvent. The typical solvents used in the production <strong>of</strong> fibers are dimethylacetamide<br />
(acrylic), acetone or chlorinated hydrocarbon (cellulose acetate), and carbon disulfide<br />
(rayon). In the dry spinning process a solution <strong>of</strong> polymer is first prepared. The solution is<br />
then heated above the boiling temperature <strong>of</strong> the solvent and the solution is extruded<br />
through spinneret. The solvent evaporates into the gas stream. With wet spinning the fiber is<br />
directly extruded into a coagulation bath where solvent diffuses into the bath liquid and the<br />
coagulant diffuses into the fiber. The fiber is washed free <strong>of</strong> solvent by passing it through an<br />
additional bath. Each process step generates emissions or wastewater. <strong>Solvents</strong> used in production<br />
are normally recovered by distillation. Figure 14.22.2 is a schematic diagram <strong>of</strong> fiber<br />
production showing that almost all stages <strong>of</strong> production generate emissions.
14.22 Polymers and man-made fibers 1017 Figure 14.22.1. Schematic diagram <strong>of</strong> emissions from the polymer manufacturing industry. [Reproduced from EPA Office <strong>of</strong> Compliance Sector Notebook Project. Pr<strong>of</strong>ile <strong>of</strong> the Petroleum Refining Industry. US Environmental Protection Agency, 1995.] vent), and residual water and solvent are purged during polymer drying. Residual solvents are removed by further drying and extrusion. <strong>Solvents</strong> are also used in equipment cleaning. <strong>Solvents</strong> are <strong>of</strong>ten stored under a nitrogen blanket to minimize oxidation and contamination. When these systems are vented solvent losses occur. Figure 14.22.1 shows a schematic diagram <strong>of</strong> potential emissions during polymer manufacture. Manufacture <strong>of</strong> man-made fibers involves polymerization (usually the core part <strong>of</strong> the process), preparation <strong>of</strong> the solution, spinning, washing and coagulation, drying and other operations. Fibers are formed by forcing the viscous liquid through small-bore orifices. A suitable viscosity can be achieved either by heating or dissolution. The rheological properties <strong>of</strong> the solution are governed to a large degree by the solvents selected. Wastes generated during the spinning operation include evaporated solvent and wastewater contaminated by solvent. The typical solvents used in the production <strong>of</strong> fibers are dimethylacetamide (acrylic), acetone or chlorinated hydrocarbon (cellulose acetate), and carbon disulfide (rayon). In the dry spinning process a solution <strong>of</strong> polymer is first prepared. The solution is then heated above the boiling temperature <strong>of</strong> the solvent and the solution is extruded through spinneret. The solvent evaporates into the gas stream. With wet spinning the fiber is directly extruded into a coagulation bath where solvent diffuses into the bath liquid and the coagulant diffuses into the fiber. The fiber is washed free <strong>of</strong> solvent by passing it through an additional bath. Each process step generates emissions or wastewater. <strong>Solvents</strong> used in production are normally recovered by distillation. Figure 14.22.2 is a schematic diagram <strong>of</strong> fiber production showing that almost all stages <strong>of</strong> production generate emissions.
1018 <strong>George</strong> <strong>Wypych</strong> Figure 14.22.2. Schematic diagram <strong>of</strong> emissions from the man-made fiber manufacturing industry. [Reproduced from EPA Office <strong>of</strong> Compliance Sector Notebook Project. Pr<strong>of</strong>ile <strong>of</strong> the Petroleum Refining Industry. US Environmental Protection Agency, 1995.] Tables 14.22.1 and 14.22.2 provide data on releases and transfers from both polymer manufacturing and man-made fiber production in the USA. Carbon disulfide, methanol, xylene, and ethylene glycol are used in the largest quantities. Carbon disulfide is used in manufacture <strong>of</strong> regenerated cellulose and rayon. Ethylene glycol is used in the manufacture <strong>of</strong> polyethylene terephthalate, the manufacture <strong>of</strong> alkyd resins, and as cosolvent for cellulose ethers and esters. Methanol is used in several processes, the largest being in the production <strong>of</strong> polyester. This industry is the 10th largest contributor <strong>of</strong> VOC and 7th largest in releases and transfers. There have been many initiatives to reduce emissions and usage <strong>of</strong> solvents. Man-made fiber manufacturing no longer uses benzene. DuPont eliminated o-xylene and reduced methanol and ethylene glycol use in its Wilmington operation. This change resulted in annual savings <strong>of</strong> $1 million. Process modification in a polymer processing plant resulted in a decrease in total emissions <strong>of</strong> 74% and a reduction in the release <strong>of</strong> cyclohexane by 96%. Monitoring <strong>of</strong> thousands <strong>of</strong> valves in Eastman Texas plant resulted in a program <strong>of</strong> valve replacement which eliminated 99% <strong>of</strong> the emissions. Plant in Florida eliminated solvents from cleaning and degreasing. These examples show that in many cases pollution can be reduced by better equipment, organization, and care.
- Page 1 and 2:
HANDBOOK OF SOLVENTS George Wypych,
- Page 3 and 4:
Preface Although the chemical indus
- Page 5 and 6:
Preface xxix contain or to have use
- Page 7 and 8:
1654 Acknowledgments 10.3 Solvent e
- Page 9 and 10:
Table of Contents Preface .........
- Page 11 and 12:
Table of contents iii 4.3 Polar sol
- Page 13 and 14:
Table of contents v 7.2.1.1 Rheolog
- Page 15 and 16:
Table of contents vii 9.4.4 Solvent
- Page 17 and 18:
Table of contents ix 12.2.2.1 Chemi
- Page 19 and 20:
Table of contents xi 14.4.3.1 Intro
- Page 21 and 22:
Table of contents xiii 14.19 Paints
- Page 23 and 24:
Table of contents xv 15.1.20 Gas ch
- Page 25 and 26:
Table of contents xvii 17.2.2 Movem
- Page 27 and 28:
Table of contents xix 18.4.7 Dry cl
- Page 29 and 30:
Table of contents xxi 20.7.1 Introd
- Page 31 and 32:
Table of contents xxiii 21.4.1.3 Pr
- Page 33 and 34:
Table of contents xxv 23.2.1.3 Sour
- Page 35 and 36:
2 Christian Reichardt aliphatic nit
- Page 37 and 38:
4 Christian Reichardt the knowledge
- Page 39 and 40:
2 Fundamental Principles Governing
- Page 41 and 42:
2.1 Solvent effects on chemical sys
- Page 43 and 44:
2.1 Solvent effects on chemical sys
- Page 45 and 46:
2.1 Solvent effects on chemical sys
- Page 47 and 48:
2.1 Solvent effects on chemical sys
- Page 49 and 50:
2.1 Solvent effects on chemical sys
- Page 51 and 52:
2.1 Solvent effects on chemical sys
- Page 53 and 54:
2.1 Solvent effects on chemical sys
- Page 55 and 56:
2.1 Solvent effects on chemical sys
- Page 57 and 58:
2.1 Solvent effects on chemical sys
- Page 59 and 60:
2.1 Solvent effects on chemical sys
- Page 61 and 62:
2.1 Solvent effects on chemical sys
- Page 63 and 64:
2.1 Solvent effects on chemical sys
- Page 65 and 66:
2.1 Solvent effects on chemical sys
- Page 67 and 68:
2.1 Solvent effects on chemical sys
- Page 69 and 70:
2.2 Molecular design of solvents 37
- Page 71 and 72:
2.2 Molecular design of solvents 39
- Page 73 and 74:
2.2 Molecular design of solvents 41
- Page 75 and 76:
2.3 Basic physical and chemical pro
- Page 77 and 78:
2.3 Basic physical and chemical pro
- Page 79 and 80:
2.3 Basic physical and chemical pro
- Page 81 and 82:
2.3 Basic physical and chemical pro
- Page 83 and 84:
2.3 Basic physical and chemical pro
- Page 85 and 86:
2.3 Basic physical and chemical pro
- Page 87 and 88:
2.3 Basic physical and chemical pro
- Page 89 and 90:
2.3 Basic physical and chemical pro
- Page 91 and 92:
2.3 Basic physical and chemical pro
- Page 93 and 94:
2.3 Basic physical and chemical pro
- Page 95 and 96:
2.3 Basic physical and chemical pro
- Page 97 and 98:
66 George Wypych Aprotic/Protic Ter
- Page 99 and 100:
68 George Wypych Biodegradability T
- Page 101 and 102:
70 George Wypych Figure 3.2.1. Sche
- Page 103 and 104:
72 George Wypych Figure 3.3.4. Simp
- Page 105 and 106:
74 George Wypych Synthetic routes a
- Page 107 and 108:
76 George Wypych Property minimum V
- Page 109 and 110:
78 George Wypych Property minimum V
- Page 111 and 112:
80 George Wypych Property minimum V
- Page 113 and 114:
82 George Wypych Property minimum V
- Page 115 and 116:
84 George Wypych Property minimum V
- Page 117 and 118:
86 George Wypych Property minimum V
- Page 119 and 120:
88 George Wypych Property minimum V
- Page 121 and 122:
90 George Wypych Property minimum V
- Page 123 and 124:
92 George Wypych Property minimum V
- Page 125 and 126:
94 George Wypych Property minimum V
- Page 127 and 128:
96 Tilman Hahn, Konrad Botzenhart,
- Page 129 and 130:
98 Tilman Hahn, Konrad Botzenhart,
- Page 131 and 132:
General Principles Governing Dissol
- Page 133 and 134:
4.1 Simple solvent characteristics
- Page 135 and 136:
4.1 Simple solvent characteristics
- Page 137 and 138:
4.1 Simple solvent characteristics
- Page 139 and 140:
4.1 Simple solvent characteristics
- Page 141 and 142:
4.1 Simple solvent characteristics
- Page 143 and 144:
4.1 Simple solvent characteristics
- Page 145 and 146:
4.1 Simple solvent characteristics
- Page 147 and 148:
4.1 Simple solvent characteristics
- Page 149 and 150:
4.1 Simple solvent characteristics
- Page 151 and 152:
4.1 Simple solvent characteristics
- Page 153 and 154:
4.1 Simple solvent characteristics
- Page 155 and 156:
4.2 Effect of system variables on s
- Page 157 and 158:
4.2 Effect of system variables on s
- Page 159 and 160:
4.2 Effect of system variables on s
- Page 161 and 162:
4.2 Effect of system variables on s
- Page 163 and 164:
4.3 Polar solvation dynamics 133 tr
- Page 165 and 166:
4.3 Polar solvation dynamics 135 Fo
- Page 167 and 168:
4.3 Polar solvation dynamics 137 at
- Page 169 and 170:
4.3 Polar solvation dynamics 139 li
- Page 171 and 172:
4.3 Polar solvation dynamics 141 Fi
- Page 173 and 174:
4.3 Polar solvation dynamics 143 Fi
- Page 175 and 176:
4.3 Polar solvation dynamics 145 ta
- Page 177 and 178:
4.4 Measurement of solvent activity
- Page 179 and 180:
4.4 Measurement of solvent activity
- Page 181 and 182:
4.4 Measurement of solvent activity
- Page 183 and 184:
4.4 Measurement of solvent activity
- Page 185 and 186:
4.4 Measurement of solvent activity
- Page 187 and 188:
4.4 Measurement of solvent activity
- Page 189 and 190:
4.4 Measurement of solvent activity
- Page 191 and 192:
4.4 Measurement of solvent activity
- Page 193 and 194:
4.4 Measurement of solvent activity
- Page 195 and 196:
4.4 Measurement of solvent activity
- Page 197 and 198:
4.4 Measurement of solvent activity
- Page 199 and 200:
4.4 Measurement of solvent activity
- Page 201 and 202:
4.4 Measurement of solvent activity
- Page 203 and 204:
4.4 Measurement of solvent activity
- Page 205 and 206:
4.4 Measurement of solvent activity
- Page 207 and 208:
4.4 Measurement of solvent activity
- Page 209 and 210:
4.4 Measurement of solvent activity
- Page 211 and 212:
4.4 Measurement of solvent activity
- Page 213 and 214:
4.4 Measurement of solvent activity
- Page 215 and 216:
4.4 Measurement of solvent activity
- Page 217 and 218:
4.4 Measurement of solvent activity
- Page 219 and 220:
4.4 Measurement of solvent activity
- Page 221 and 222:
4.4 Measurement of solvent activity
- Page 223 and 224:
4.4 Measurement of solvent activity
- Page 225 and 226:
4.4 Measurement of solvent activity
- Page 227 and 228:
4.4 Measurement of solvent activity
- Page 229 and 230:
4.4 Measurement of solvent activity
- Page 231 and 232:
4.4 Measurement of solvent activity
- Page 233 and 234:
4.4 Measurement of solvent activity
- Page 235 and 236:
4.4 Measurement of solvent activity
- Page 237 and 238:
4.4 Measurement of solvent activity
- Page 239 and 240:
4.4 Measurement of solvent activity
- Page 241 and 242:
4.4 Measurement of solvent activity
- Page 243 and 244:
4.4 Measurement of solvent activity
- Page 245 and 246:
4.4 Measurement of solvent activity
- Page 247 and 248:
4.4 Measurement of solvent activity
- Page 249 and 250:
4.4 Measurement of solvent activity
- Page 251 and 252:
4.4 Measurement of solvent activity
- Page 253 and 254:
4.4 Measurement of solvent activity
- Page 255 and 256:
4.4 Measurement of solvent activity
- Page 257 and 258:
4.4 Measurement of solvent activity
- Page 259 and 260:
4.4 Measurement of solvent activity
- Page 261 and 262:
4.4 Measurement of solvent activity
- Page 263 and 264:
4.4 Measurement of solvent activity
- Page 265 and 266:
4.4 Measurement of solvent activity
- Page 267 and 268:
4.4 Measurement of solvent activity
- Page 269 and 270:
4.4 Measurement of solvent activity
- Page 271 and 272:
4.4 Measurement of solvent activity
- Page 273 and 274:
Solubility of Selected Systems and
- Page 275 and 276:
5.1 Solubility parameters 245 ln P
- Page 277 and 278:
5.1 Solubility parameters 247 Accep
- Page 279 and 280:
5.1 Solubility parameters 249 media
- Page 281 and 282:
5.1 Solubility parameters 251 Polym
- Page 283 and 284:
5.2 Prediction of solubility parame
- Page 285 and 286:
5.2 Prediction of solubility parame
- Page 287 and 288:
5.2 Prediction of solubility parame
- Page 289 and 290:
5.2 Prediction of solubility parame
- Page 291 and 292:
5.3 Methods of calculation of solub
- Page 293 and 294:
5.3 Methods of calculation of solub
- Page 295 and 296:
5.3 Methods of calculation of solub
- Page 297 and 298:
5.4 Mixed solvents - polymer solubi
- Page 299 and 300:
5.4 Mixed solvents - polymer solubi
- Page 301 and 302:
5.4 Mixed solvents - polymer solubi
- Page 303 and 304:
5.4 Mixed solvents - polymer solubi
- Page 305 and 306:
5.4 Mixed solvents - polymer solubi
- Page 307 and 308:
5.4 Mixed solvents - polymer solubi
- Page 309 and 310:
5.4 Mixed solvents - polymer solubi
- Page 311 and 312:
5.5 The phenomenological theory of
- Page 313 and 314:
5.5 The phenomenological theory of
- Page 315 and 316:
5.5 The phenomenological theory of
- Page 317 and 318:
5.5 The phenomenological theory of
- Page 319 and 320:
5.5 The phenomenological theory of
- Page 321 and 322:
5.5 The phenomenological theory of
- Page 323 and 324:
5.5 The phenomenological theory of
- Page 325 and 326:
5.5 The phenomenological theory of
- Page 327 and 328:
5.5 The phenomenological theory of
- Page 329 and 330:
5.5 The phenomenological theory of
- Page 331 and 332:
5.5 The phenomenological theory of
- Page 333 and 334:
5.5 The phenomenological theory of
- Page 335 and 336:
306 E. Ya. Denisyuk, V. V. Tereshat
- Page 337 and 338:
308 E. Ya. Denisyuk, V. V. Tereshat
- Page 339 and 340:
310 E. Ya. Denisyuk, V. V. Tereshat
- Page 341 and 342:
312 E. Ya. Denisyuk, V. V. Tereshat
- Page 343 and 344:
314 E. Ya. Denisyuk, V. V. Tereshat
- Page 345 and 346:
316 E. Ya. Denisyuk, V. V. Tereshat
- Page 347 and 348:
318 V V Tereshatov, V Yu. Senichev,
- Page 349 and 350:
320 V V Tereshatov, V Yu. Senichev,
- Page 351 and 352:
322 V V Tereshatov, V Yu. Senichev,
- Page 353 and 354:
324 V V Tereshatov, V Yu. Senichev,
- Page 355 and 356:
326 V V Tereshatov, V Yu. Senichev,
- Page 357 and 358:
328 Vasiliy V. Tereshatov, Valery Y
- Page 359 and 360:
330 Vasiliy V. Tereshatov, Valery Y
- Page 361 and 362:
332 Vasiliy V. Tereshatov, Valery Y
- Page 363 and 364:
334 Vasiliy V. Tereshatov, Valery Y
- Page 365 and 366:
336 Vasiliy V. Tereshatov, Valery Y
- Page 367 and 368:
338 Vasiliy V. Tereshatov, Valery Y
- Page 369 and 370:
340 George Wypych where: τM the mo
- Page 371 and 372:
342 George Wypych ξ 0.55 0.5 0.45
- Page 373 and 374:
344 George Wypych Self-diffusion co
- Page 375 and 376:
346 George Wypych Temperature, K 31
- Page 377 and 378:
348 George Wypych Diffusion distanc
- Page 379 and 380:
350 George Wypych • evaporation-i
- Page 381 and 382:
352 George Wypych Water volume frac
- Page 383 and 384:
354 George Wypych Diffusion coeffic
- Page 385 and 386:
356 Semyon Levitsky, Zinoviy Shulma
- Page 387 and 388:
358 Semyon Levitsky, Zinoviy Shulma
- Page 389 and 390:
360 Semyon Levitsky, Zinoviy Shulma
- Page 391 and 392:
362 Semyon Levitsky, Zinoviy Shulma
- Page 393 and 394:
364 Semyon Levitsky, Zinoviy Shulma
- Page 395 and 396:
366 Semyon Levitsky, Zinoviy Shulma
- Page 397 and 398:
368 Semyon Levitsky, Zinoviy Shulma
- Page 399 and 400:
370 Semyon Levitsky, Zinoviy Shulma
- Page 401 and 402:
372 Semyon Levitsky, Zinoviy Shulma
- Page 403 and 404:
374 Semyon Levitsky, Zinoviy Shulma
- Page 405 and 406:
376 Semyon Levitsky, Zinoviy Shulma
- Page 407 and 408:
378 Semyon Levitsky, Zinoviy Shulma
- Page 409 and 410:
380 Semyon Levitsky, Zinoviy Shulma
- Page 411 and 412:
382 Semyon Levitsky, Zinoviy Shulma
- Page 413 and 414:
384 Semyon Levitsky, Zinoviy Shulma
- Page 415 and 416:
386 Seung Su Kim, Jae Chun Hyun 7.3
- Page 417 and 418:
388 Seung Su Kim, Jae Chun Hyun rat
- Page 419 and 420:
390 Seung Su Kim, Jae Chun Hyun The
- Page 421 and 422:
392 Seung Su Kim, Jae Chun Hyun whe
- Page 423 and 424:
394 Seung Su Kim, Jae Chun Hyun beg
- Page 425 and 426:
396 Seung Su Kim, Jae Chun Hyun 7.3
- Page 427 and 428:
398 Seung Su Kim, Jae Chun Hyun Fig
- Page 429 and 430:
400 Seung Su Kim, Jae Chun Hyun Fig
- Page 431 and 432:
402 Seung Su Kim, Jae Chun Hyun Fig
- Page 433 and 434:
404 Seung Su Kim, Jae Chun Hyun sol
- Page 435 and 436:
406 Seung Su Kim, Jae Chun Hyun Tab
- Page 437 and 438:
408 Seung Su Kim, Jae Chun Hyun and
- Page 439 and 440:
410 Seung Su Kim, Jae Chun Hyun to
- Page 441 and 442:
412 Seung Su Kim, Jae Chun Hyun The
- Page 443 and 444:
414 Seung Su Kim, Jae Chun Hyun cau
- Page 445 and 446:
416 Seung Su Kim, Jae Chun Hyun Nu
- Page 447 and 448:
Interactions in Solvents and Soluti
- Page 449 and 450:
8.2 Basic simplifications of quantu
- Page 451 and 452:
8.2 Basic simplifications of quantu
- Page 453 and 454:
8.4 Two-body interaction energy 425
- Page 455 and 456:
8.4 Two-body interaction energy 427
- Page 457 and 458:
8.4 Two-body interaction energy 429
- Page 459 and 460:
8.4 Two-body interaction energy 431
- Page 461 and 462:
8.4 Two-body interaction energy 433
- Page 463 and 464:
8.4 Two-body interaction energy 435
- Page 465 and 466:
8.4 Two-body interaction energy 437
- Page 467 and 468:
8.4 Two-body interaction energy 439
- Page 469 and 470:
8.4 Two-body interaction energy 441
- Page 471 and 472:
8.4 Two-body interaction energy 443
- Page 473 and 474:
8.4 Two-body interaction energy 445
- Page 475 and 476:
8.4 Two-body interaction energy 447
- Page 477 and 478:
8.4 Two-body interaction energy 449
- Page 479 and 480:
8.5 Three- and many-body interactio
- Page 481 and 482:
8.5 Three- and many-body interactio
- Page 483 and 484:
8.5 Three- and many-body interactio
- Page 485 and 486:
8.6 The variety of interaction pote
- Page 487 and 488:
8.6 The variety of interaction pote
- Page 489 and 490:
8.7 Theoretical and computing model
- Page 491 and 492:
8.7 Theoretical and computing model
- Page 493 and 494:
8.7 Theoretical and computing model
- Page 495 and 496:
8.7 Theoretical and computing model
- Page 497 and 498:
8.7 Theoretical and computing model
- Page 499 and 500:
8.7 Theoretical and computing model
- Page 501 and 502:
8.7 Theoretical and computing model
- Page 503 and 504:
8.7 Theoretical and computing model
- Page 505 and 506:
8.7 Theoretical and computing model
- Page 507 and 508:
8.7 Theoretical and computing model
- Page 509 and 510:
8.7 Theoretical and computing model
- Page 511 and 512:
8.7 Theoretical and computing model
- Page 513 and 514:
8.7 Theoretical and computing model
- Page 515 and 516:
8.8 Practical applications of model
- Page 517 and 518:
8.8 Practical applications of model
- Page 519 and 520:
8.8 Practical applications of model
- Page 521 and 522:
8.9 Liquid surfaces 493 to study th
- Page 523 and 524:
8.9 Liquid surfaces 495 The potenti
- Page 525 and 526:
8.9 Liquid surfaces 497 out of equi
- Page 527 and 528:
8.9 Liquid surfaces 499 tions) of t
- Page 529 and 530:
8 Interactions in solvents and solu
- Page 531 and 532:
8 Interactions in solvents and solu
- Page 533 and 534:
9 Mixed Solvents Y. Y. Fialkov, V.
- Page 535 and 536:
9.2 Chemical interaction between co
- Page 537 and 538:
9.2 Chemical interaction between co
- Page 539 and 540:
9.3 Physical properties of mixed so
- Page 541 and 542:
9.3 Physical properties of mixed so
- Page 543 and 544:
9.3 Physical properties of mixed so
- Page 545 and 546:
9.3 Physical properties of mixed so
- Page 547 and 548:
9.3 Physical properties of mixed so
- Page 549 and 550:
9.3 Physical properties of mixed so
- Page 551 and 552:
9.3 Physical properties of mixed so
- Page 553 and 554:
9.3 Physical properties of mixed so
- Page 555 and 556:
9.4 Mixed solvent influence on the
- Page 557 and 558:
9.4 Mixed solvent influence on the
- Page 559 and 560:
9.4 Mixed solvent influence on the
- Page 561 and 562:
9.4 Mixed solvent influence on the
- Page 563 and 564:
9.4 Mixed solvent influence on the
- Page 565 and 566:
9.4 Mixed solvent influence on the
- Page 567 and 568:
9.4 Mixed solvent influence on the
- Page 569 and 570:
9.4 Mixed solvent influence on the
- Page 571 and 572:
9.4 Mixed solvent influence on the
- Page 573 and 574:
9.4 Mixed solvent influence on the
- Page 575 and 576:
9.4 Mixed solvent influence on the
- Page 577 and 578:
9.4 Mixed solvent influence on the
- Page 579 and 580:
9.4 Mixed solvent influence on the
- Page 581 and 582:
9.4 Mixed solvent influence on the
- Page 583 and 584:
9.4 Mixed solvent influence on the
- Page 585 and 586:
9.5 The mixed solvent effect on the
- Page 587 and 588:
9.5 The mixed solvent effect on the
- Page 589 and 590:
9.5 The mixed solvent effect on the
- Page 591 and 592:
9 Mixed solvents 563 22 Minkin V.,
- Page 593 and 594:
10 Acid-base Interactions 10.1 GENE
- Page 595 and 596:
10.1 General concept of acid-base i
- Page 597 and 598:
10.1 General concept of acid-base i
- Page 599 and 600:
10.2 Effect of polymer/solvent acid
- Page 601 and 602:
10.2 Effect of polymer/solvent acid
- Page 603 and 604:
10.2 Effect of polymer/solvent acid
- Page 605 and 606:
10.2 Effect of polymer/solvent acid
- Page 607 and 608:
10.2 Effect of polymer/solvent acid
- Page 609 and 610:
10.2 Effect of polymer/solvent acid
- Page 611 and 612:
10.3 Solvent effects based on pure
- Page 613 and 614:
10.3 Solvent effects based on pure
- Page 615 and 616:
10.3 Solvent effects based on pure
- Page 617 and 618:
10.3 Solvent effects based on pure
- Page 619 and 620:
10.3 Solvent effects based on pure
- Page 621 and 622:
10.3 Solvent effects based on pure
- Page 623 and 624:
10.3 Solvent effects based on pure
- Page 625 and 626:
10.3 Solvent effects based on pure
- Page 627 and 628:
10.3 Solvent effects based on pure
- Page 629 and 630:
10.3 Solvent effects based on pure
- Page 631 and 632:
10.3 Solvent effects based on pure
- Page 633 and 634:
10.3 Solvent effects based on pure
- Page 635 and 636:
10.3 Solvent effects based on pure
- Page 637 and 638:
10.3 Solvent effects based on pure
- Page 639 and 640:
10.3 Solvent effects based on pure
- Page 641 and 642:
10.3 Solvent effects based on pure
- Page 643 and 644:
10.3 Solvent effects based on pure
- Page 645 and 646:
10.4 Acid-base equilibria in ionic
- Page 647 and 648:
10.4 Acid-base equilibria in ionic
- Page 649 and 650:
10.4 Acid-base equilibria in ionic
- Page 651 and 652:
10.4 Acid-base equilibria in ionic
- Page 653 and 654:
10.4 Acid-base equilibria in ionic
- Page 655 and 656:
10.4 Acid-base equilibria in ionic
- Page 657 and 658:
10.4 Acid-base equilibria in ionic
- Page 659 and 660:
10.4 Acid-base equilibria in ionic
- Page 661 and 662:
10.4 Acid-base equilibria in ionic
- Page 663 and 664:
10.4 Acid-base equilibria in ionic
- Page 665 and 666:
10.4 Acid-base equilibria in ionic
- Page 667 and 668:
11 Electronic and Electrical Effect
- Page 669 and 670:
11.1 Theoretical treatment of solve
- Page 671 and 672:
11.1 Theoretical treatment of solve
- Page 673 and 674:
11.1 Theoretical treatment of solve
- Page 675 and 676:
11.1 Theoretical treatment of solve
- Page 677 and 678:
11.1 Theoretical treatment of solve
- Page 679 and 680:
11.1 Theoretical treatment of solve
- Page 681 and 682:
11.1 Theoretical treatment of solve
- Page 683 and 684:
11.1 Theoretical treatment of solve
- Page 685 and 686:
11.1 Theoretical treatment of solve
- Page 687 and 688:
11.1 Theoretical treatment of solve
- Page 689 and 690:
11.1 Theoretical treatment of solve
- Page 691 and 692:
11.1 Theoretical treatment of solve
- Page 693 and 694:
11.1 Theoretical treatment of solve
- Page 695 and 696:
11.1 Theoretical treatment of solve
- Page 697 and 698:
11.1 Theoretical treatment of solve
- Page 699 and 700:
11.1 Theoretical treatment of solve
- Page 701 and 702:
11.1 Theoretical treatment of solve
- Page 703 and 704:
11.1 Theoretical treatment of solve
- Page 705 and 706:
11.1 Theoretical treatment of solve
- Page 707 and 708:
11.1 Theoretical treatment of solve
- Page 709 and 710:
11.2 Dielectric solvent effects 681
- Page 711 and 712:
12 Other Properties of Solvents, So
- Page 713 and 714:
12.1 Rheological properties, aggreg
- Page 715 and 716:
12.1 Rheological properties, aggreg
- Page 717 and 718:
12.1 Rheological properties, aggreg
- Page 719 and 720:
12.1 Rheological properties, aggreg
- Page 721 and 722:
12.1 Rheological properties, aggreg
- Page 723 and 724:
12.1 Rheological properties, aggreg
- Page 725 and 726:
12.1 Rheological properties, aggreg
- Page 727 and 728:
12.1 Rheological properties, aggreg
- Page 729 and 730:
12.1 Rheological properties, aggreg
- Page 731 and 732:
12.1 Rheological properties, aggreg
- Page 733 and 734:
12.1 Rheological properties, aggreg
- Page 735 and 736:
12.2 Chain conformations of polysac
- Page 737 and 738:
12.2 Chain conformations of polysac
- Page 739 and 740:
12.2 Chain conformations of polysac
- Page 741 and 742:
12.2 Chain conformations of polysac
- Page 743 and 744:
12.2 Chain conformations of polysac
- Page 745 and 746:
12.2 Chain conformations of polysac
- Page 747 and 748:
12.2 Chain conformations of polysac
- Page 749 and 750:
12.2 Chain conformations of polysac
- Page 751 and 752:
12.2 Chain conformations of polysac
- Page 753 and 754:
12.2 Chain conformations of polysac
- Page 755 and 756:
12.2 Chain conformations of polysac
- Page 757 and 758:
12.2 Chain conformations of polysac
- Page 759 and 760:
12.2 Chain conformations of polysac
- Page 761 and 762:
12.2 Chain conformations of polysac
- Page 763 and 764:
12.2 Chain conformations of polysac
- Page 765 and 766:
738 Roland Schmid Figure 13.1.1. Re
- Page 767 and 768:
740 Roland Schmid HB interactions,
- Page 769 and 770:
742 Roland Schmid AN = -133.8 - 0.0
- Page 771 and 772:
744 Roland Schmid ated by the macro
- Page 773 and 774:
746 Roland Schmid turns out, polar
- Page 775 and 776:
748 Roland Schmid Packing density
- Page 777 and 778:
750 Roland Schmid tween calculated
- Page 779 and 780:
752 Roland Schmid over the solute-s
- Page 781 and 782:
754 Roland Schmid of the empirical
- Page 783 and 784:
756 Roland Schmid From X-ray and ne
- Page 785 and 786:
758 Roland Schmid Table 13.1.5. Sol
- Page 787 and 788:
760 Roland Schmid ΔG = ΔG + ΔG [
- Page 789 and 790:
762 Roland Schmid very recent paper
- Page 791 and 792:
764 Roland Schmid Solvent ΔvH/RT
- Page 793 and 794:
766 Roland Schmid E r = E i + E s [
- Page 795 and 796:
768 Roland Schmid from the explicit
- Page 797 and 798:
770 Roland Schmid sequently, there
- Page 799 and 800:
772 Roland Schmid simulations. 188-
- Page 801 and 802:
774 Roland Schmid 23 N. A. Lewis, Y
- Page 803 and 804:
776 Roland Schmid 132 R. R. Dogonad
- Page 805 and 806:
778 Michelle L. Coote and Thomas P.
- Page 807 and 808:
780 Michelle L. Coote and Thomas P.
- Page 809 and 810:
782 Michelle L. Coote and Thomas P.
- Page 811 and 812:
784 Michelle L. Coote and Thomas P.
- Page 813 and 814:
786 Michelle L. Coote and Thomas P.
- Page 815 and 816:
788 Michelle L. Coote and Thomas P.
- Page 817 and 818:
790 Michelle L. Coote and Thomas P.
- Page 819 and 820:
792 Michelle L. Coote and Thomas P.
- Page 821 and 822:
794 Michelle L. Coote and Thomas P.
- Page 823 and 824:
796 Michelle L. Coote and Thomas P.
- Page 825 and 826:
798 Maw-Ling Wang 13.3 EFFECTS OF O
- Page 827 and 828:
800 Maw-Ling Wang [13.3.2] Inverse
- Page 829 and 830:
802 Maw-Ling Wang Both cation and a
- Page 831 and 832:
804 Maw-Ling Wang Table 13.3.2. Eff
- Page 833 and 834:
806 Maw-Ling Wang Table 13.3.3. Ext
- Page 835 and 836:
808 Maw-Ling Wang Table 13.3.5. Eff
- Page 837 and 838:
810 Maw-Ling Wang reacts with pheno
- Page 839 and 840:
812 Maw-Ling Wang Figure 13.3.3. Ef
- Page 841 and 842:
814 Maw-Ling Wang the organic solve
- Page 843 and 844:
816 Maw-Ling Wang crease. Therefore
- Page 845 and 846:
818 Maw-Ling Wang (F) Polymerizatio
- Page 847 and 848:
820 Maw-Ling Wang Table 13.3.16. Sy
- Page 849 and 850:
822 Maw-Ling Wang 13.3.1.4 Effect o
- Page 851 and 852:
824 Maw-Ling Wang Table 13.3.19 Eff
- Page 853 and 854:
826 Maw-Ling Wang quaternary salt c
- Page 855 and 856:
828 Maw-Ling Wang Table 13.3.24. Ef
- Page 857 and 858:
830 Maw-Ling Wang Solvent Dielectri
- Page 859 and 860:
832 Maw-Ling Wang ied. 82,83,97,101
- Page 861 and 862:
834 Maw-Ling Wang substitution, suc
- Page 863 and 864:
836 Maw-Ling Wang (2) the ion excha
- Page 865 and 866:
838 Maw-Ling Wang REFERENCES 1 A. A
- Page 867 and 868:
840 Maw-Ling Wang 101 D. C. Sherrin
- Page 869 and 870:
842 Norio Tsubokawa [13.4.2] PAI is
- Page 871 and 872:
844 Norio Tsubokawa Table 13.4.2. I
- Page 873 and 874:
846 Norio Tsubokawa more easily tha
- Page 875 and 876:
848 George Wypych methyl amyl keton
- Page 877 and 878:
850 George Wypych Peel strength, N/
- Page 879 and 880:
852 George Wypych 8 P Enenkel, H Ba
- Page 881 and 882:
854 George Wypych Table 14.2.2. Tot
- Page 883 and 884:
856 M Matsumoto, S Isken, JAMdeBont
- Page 885 and 886:
858 M Matsumoto, S Isken, JAMdeBont
- Page 887 and 888:
860 M Matsumoto, S Isken, JAMdeBont
- Page 889 and 890:
862 M Matsumoto, S Isken, JAMdeBont
- Page 891 and 892:
864 M Matsumoto, S Isken, JAMdeBont
- Page 893 and 894:
866 Tilman Hahn, Konrad Botzenhart
- Page 895 and 896:
868 Tilman Hahn, Konrad Botzenhart
- Page 897 and 898:
870 Tilman Hahn, Konrad Botzenhart
- Page 899 and 900:
872 Tsuneo Yamane 14.4.3 CHOICE OF
- Page 901 and 902:
874 Tsuneo Yamane Very trace amount
- Page 903 and 904:
876 Tsuneo Yamane It has been shown
- Page 905 and 906:
878 Tsuneo Yamane [ ( kcat Km) ( kc
- Page 907 and 908:
880 George Wypych 11 A. Zaks, in En
- Page 909 and 910:
882 George Wypych rected towards im
- Page 911 and 912:
884 Kaspar D. Hasenclever than 55°
- Page 913 and 914:
886 Kaspar D. Hasenclever The same
- Page 915 and 916:
888 Kaspar D. Hasenclever Figure 14
- Page 917 and 918:
890 Kaspar D. Hasenclever Computer
- Page 919 and 920:
892 Kaspar D. Hasenclever • Solve
- Page 921 and 922:
894 Martin Hanek, Norbert Löw, And
- Page 923 and 924:
896 Martin Hanek, Norbert Löw, And
- Page 925 and 926:
898 Martin Hanek, Norbert Löw, And
- Page 927 and 928:
900 Martin Hanek, Norbert Löw, And
- Page 929 and 930:
902 Martin Hanek, Norbert Löw, And
- Page 931 and 932:
904 Martin Hanek, Norbert Löw, And
- Page 933 and 934:
906 Martin Hanek, Norbert Löw, And
- Page 935 and 936:
908 Martin Hanek, Norbert Löw, And
- Page 937 and 938:
910 Martin Hanek, Norbert Löw, And
- Page 939 and 940:
912 Martin Hanek, Norbert Löw, And
- Page 941 and 942:
914 Martin Hanek, Norbert Löw, And
- Page 943 and 944:
916 Martin Hanek, Norbert Löw, And
- Page 945 and 946:
918 Martin Hanek, Norbert Löw, And
- Page 947 and 948:
920 George Wypych 20 N. L�w, EPP
- Page 949 and 950:
922 George Wypych Table 14.9.2. Rep
- Page 951 and 952:
924 Phillip J. Wakelyn, Peter J. Wa
- Page 953 and 954:
926 Phillip J. Wakelyn, Peter J. Wa
- Page 955 and 956:
928 Phillip J. Wakelyn, Peter J. Wa
- Page 957 and 958:
930 Phillip J. Wakelyn, Peter J. Wa
- Page 959 and 960:
932 Phillip J. Wakelyn, Peter J. Wa
- Page 961 and 962:
934 Phillip J. Wakelyn, Peter J. Wa
- Page 963 and 964:
936 Phillip J. Wakelyn, Peter J. Wa
- Page 965 and 966:
938 Phillip J. Wakelyn, Peter J. Wa
- Page 967 and 968:
940 Phillip J. Wakelyn, Peter J. Wa
- Page 969 and 970:
942 Phillip J. Wakelyn, Peter J. Wa
- Page 971 and 972:
944 Phillip J. Wakelyn, Peter J. Wa
- Page 973 and 974:
946 Phillip J. Wakelyn, Peter J. Wa
- Page 975 and 976:
948 Phillip J. Wakelyn, Peter J. Wa
- Page 977 and 978:
950 George Wypych 14.11 GROUND TRAN
- Page 979 and 980:
952 George Wypych Figure 14.13.1. S
- Page 981 and 982:
954 Tilman Hahn, Konrad Botzenhart,
- Page 983 and 984:
956 George Wypych more to show that
- Page 985 and 986:
958 George Wypych Table 14.16.1. Re
- Page 987 and 988:
960 George Wypych Table 14.17.1. Re
- Page 989 and 990:
962 George Wypych Table 14.18.2. Re
- Page 991 and 992:
964 Tilman Hahn, Konrad Botzenhart,
- Page 993 and 994: 966 Tilman Hahn, Konrad Botzenhart,
- Page 995 and 996: 968 Tilman Hahn, Konrad Botzenhart,
- Page 997 and 998: 970 David Randall 14.19.2.2 Water b
- Page 999 and 1000: 972 David Randall Hydrophobic subst
- Page 1001 and 1002: 974 David Randall 50-60% glutaric,
- Page 1003 and 1004: 976 George Wypych Figure 14.20.1. D
- Page 1005 and 1006: 978 Michel Bauer, Christine Barthé
- Page 1007 and 1008: 980 Michel Bauer, Christine Barthé
- Page 1009 and 1010: 982 Michel Bauer, Christine Barthé
- Page 1011 and 1012: 984 Michel Bauer, Christine Barthé
- Page 1013 and 1014: 986 Michel Bauer, Christine Barthé
- Page 1015 and 1016: 988 Michel Bauer, Christine Barthé
- Page 1017 and 1018: 990 Michel Bauer, Christine Barthé
- Page 1019 and 1020: 992 Michel Bauer, Christine Barthé
- Page 1021 and 1022: 994 Michel Bauer, Christine Barthé
- Page 1023 and 1024: 996 Michel Bauer, Christine Barthé
- Page 1025 and 1026: 998 An Li This discussion is intend
- Page 1027 and 1028: 1000 An Li Trade Name Cosolvent vol
- Page 1029 and 1030: 1002 An Li Figure 14.21.2.1. Effect
- Page 1031 and 1032: 1004 An Li partial derivative ∂(l
- Page 1033 and 1034: 1006 An Li Equation [14.21.2.8] can
- Page 1035 and 1036: 1008 An Li Figure 14.21.2.2a. Devia
- Page 1037 and 1038: 1010 An Li Figure 14.21.2.2c. Devia
- Page 1039 and 1040: 1012 An Li f 0.1 0.2 0.4 0.6 0.8 0.
- Page 1041 and 1042: 1014 An Li estimated from the log K
- Page 1043: 1016 George Wypych 72 K. Brololm, a
- Page 1047 and 1048: 1020 George Wypych New technology i
- Page 1049 and 1050: 1022 George Wypych Table 14.23.1. R
- Page 1051 and 1052: 1024 George Wypych Table 14.24.2. R
- Page 1053 and 1054: 1026 Mohamed Serageldin, Dave Reeve
- Page 1055 and 1056: 1028 Mohamed Serageldin, Dave Reeve
- Page 1057 and 1058: 1030 Mohamed Serageldin, Dave Reeve
- Page 1059 and 1060: 1032 Mohamed Serageldin, Dave Reeve
- Page 1061 and 1062: 1034 Mohamed Serageldin, Dave Reeve
- Page 1063 and 1064: 1036 Mohamed Serageldin, Dave Reeve
- Page 1065 and 1066: 1038 Mohamed Serageldin, Dave Reeve
- Page 1067 and 1068: 1040 George Wypych Table 14.27.2. R
- Page 1069 and 1070: 1042 George Wypych Table 14.28.2. R
- Page 1071 and 1072: 1044 George Wypych Table 14.31.1. R
- Page 1073 and 1074: 1046 George Wypych Table 14.32.1. R
- Page 1075 and 1076: 1048 George Wypych Table 14.32.3. R
- Page 1077 and 1078: 1050 George Wypych Table 14.32.5. T
- Page 1079 and 1080: 1052 George Wypych The traditional
- Page 1081 and 1082: 1054 George Wypych The acidity of b
- Page 1083 and 1084: 1056 George Wypych except water whi
- Page 1085 and 1086: 1058 George Wypych solution is 2.73
- Page 1087 and 1088: 1060 George Wypych presence of igni
- Page 1089 and 1090: 1062 George Wypych method of determ
- Page 1091 and 1092: 1064 George Wypych used. A thermal
- Page 1093 and 1094: 1066 George Wypych 15.1.26 REFRACTI
- Page 1095 and 1096:
1068 George Wypych Table 15.1.1. Ty
- Page 1097 and 1098:
1070 George Wypych Wexcluded solven
- Page 1099 and 1100:
1072 George Wypych 25 ASTM D 2108-9
- Page 1101 and 1102:
1074 George Wypych 68 ASTM D 3844-9
- Page 1103 and 1104:
1076 George Wypych BS 506-2.84. Met
- Page 1105 and 1106:
1078 Myrto Petreas 15.2 SPECIAL MET
- Page 1107 and 1108:
1080 Myrto Petreas In short, biolog
- Page 1109 and 1110:
1082 Myrto Petreas cients of some i
- Page 1111 and 1112:
1084 Myrto Petreas lection at the a
- Page 1113 and 1114:
1086 Myrto Petreas and legal reperc
- Page 1115 and 1116:
1088 Myrto Petreas • The solvent
- Page 1117 and 1118:
1090 Myrto Petreas of time after ex
- Page 1119 and 1120:
1092 Myrto Petreas even after log-l
- Page 1121 and 1122:
1094 Myrto Petreas 26 M Petreas, J
- Page 1123 and 1124:
1096 James L. Botsford In Europe ma
- Page 1125 and 1126:
1098 James L. Botsford Figure 15.2.
- Page 1127 and 1128:
1100 James L. Botsford cussed. Neit
- Page 1129 and 1130:
1102 James L. Botsford n Ave. Var.
- Page 1131 and 1132:
1104 James L. Botsford (Calleja et
- Page 1133 and 1134:
1106 James L. Botsford Table 15.2.2
- Page 1135 and 1136:
1108 James L. Botsford the test is
- Page 1137 and 1138:
1110 James L. Botsford Table 15.2.2
- Page 1139 and 1140:
1112 James L. Botsford Geiger, D. L
- Page 1141 and 1142:
1114 Christine Barthélémy, Michel
- Page 1143 and 1144:
1116 Christine Barthélémy, Michel
- Page 1145 and 1146:
1118 Christine Barthélémy, Michel
- Page 1147 and 1148:
1120 Christine Barthélémy, Michel
- Page 1149 and 1150:
1122 Christine Barthélémy, Michel
- Page 1151 and 1152:
1124 Christine Barthélémy, Michel
- Page 1153 and 1154:
1126 George Wypych n-heptane molecu
- Page 1155 and 1156:
1128 George Wypych MEK P PA Fat-fre
- Page 1157 and 1158:
1130 Michel Bauer, Christine Barth
- Page 1159 and 1160:
1132 Michel Bauer, Christine Barth
- Page 1161 and 1162:
1134 Michel Bauer, Christine Barth
- Page 1163 and 1164:
1136 Michel Bauer, Christine Barth
- Page 1165 and 1166:
1138 Michel Bauer, Christine Barth
- Page 1167 and 1168:
1140 Michel Bauer, Christine Barth
- Page 1169 and 1170:
1142 Michel Bauer, Christine Barth
- Page 1171 and 1172:
1144 Michel Bauer, Christine Barth
- Page 1173 and 1174:
1146 Michel Bauer, Christine Barth
- Page 1175 and 1176:
17 Environmental Impact of Solvents
- Page 1177 and 1178:
17.1 The environmental fate and mov
- Page 1179 and 1180:
17.1 The environmental fate and mov
- Page 1181 and 1182:
17.1 The environmental fate and mov
- Page 1183 and 1184:
17.1 The environmental fate and mov
- Page 1185 and 1186:
17.1 The environmental fate and mov
- Page 1187 and 1188:
17.1 The environmental fate and mov
- Page 1189 and 1190:
17.2 Fate-based management 1163 dat
- Page 1191 and 1192:
17.2 Fate-based management 1165 bre
- Page 1193 and 1194:
17.2 Fate-based management 1167 gra
- Page 1195 and 1196:
17.3 Environmental fate of glycol e
- Page 1197 and 1198:
17.3 Environmental fate of glycol e
- Page 1199 and 1200:
17.3 Environmental fate of glycol e
- Page 1201 and 1202:
17.3 Environmental fate of glycol e
- Page 1203 and 1204:
17.3 Environmental fate of glycol e
- Page 1205 and 1206:
17.3 Environmental fate of glycol e
- Page 1207 and 1208:
17.3 Environmental fate of glycol e
- Page 1209 and 1210:
17.3 Environmental fate of glycol e
- Page 1211 and 1212:
17.3 Environmental fate of glycol e
- Page 1213 and 1214:
17.3 Environmental fate of glycol e
- Page 1215 and 1216:
17.4 Organic solvent impacts on tro
- Page 1217 and 1218:
17.4 Organic solvent impacts on tro
- Page 1219 and 1220:
17.4 Organic solvent impacts on tro
- Page 1221 and 1222:
17.4 Organic solvent impacts on tro
- Page 1223 and 1224:
17.4 Organic solvent impacts on tro
- Page 1225 and 1226:
17.4 Organic solvent impacts on tro
- Page 1227 and 1228:
18 Concentration of Solvents in Var
- Page 1229 and 1230:
18.1 Measurement and estimation of
- Page 1231 and 1232:
18.1 Measurement and estimation of
- Page 1233 and 1234:
18.1 Measurement and estimation of
- Page 1235 and 1236:
18.1 Measurement and estimation of
- Page 1237 and 1238:
18.1 Measurement and estimation of
- Page 1239 and 1240:
18.1 Measurement and estimation of
- Page 1241 and 1242:
18.1 Measurement and estimation of
- Page 1243 and 1244:
18.1 Measurement and estimation of
- Page 1245 and 1246:
18.1 Measurement and estimation of
- Page 1247 and 1248:
18.1 Measurement and estimation of
- Page 1249 and 1250:
18.1 Measurement and estimation of
- Page 1251 and 1252:
18.1 Measurement and estimation of
- Page 1253 and 1254:
18.2 Prediction of organic solvents
- Page 1255 and 1256:
18.2 Prediction of organic solvents
- Page 1257 and 1258:
18.2 Prediction of organic solvents
- Page 1259 and 1260:
18.2 Prediction of organic solvents
- Page 1261 and 1262:
18.3 Indoor air pollution by solven
- Page 1263 and 1264:
18.3 Indoor air pollution by solven
- Page 1265 and 1266:
18.3 Indoor air pollution by solven
- Page 1267 and 1268:
18.3 Indoor air pollution by solven
- Page 1269 and 1270:
18.3 Indoor air pollution by solven
- Page 1271 and 1272:
18.3 Indoor air pollution by solven
- Page 1273 and 1274:
18.3 Indoor air pollution by solven
- Page 1275 and 1276:
18.3 Indoor air pollution by solven
- Page 1277 and 1278:
18.4 Solvent uses with exposure ris
- Page 1279 and 1280:
18.4 Solvent uses with exposure ris
- Page 1281 and 1282:
18.4 Solvent uses with exposure ris
- Page 1283 and 1284:
18.4 Solvent uses with exposure ris
- Page 1285 and 1286:
18.4 Solvent uses with exposure ris
- Page 1287 and 1288:
18.4 Solvent uses with exposure ris
- Page 1289 and 1290:
18.4 Solvent uses with exposure ris
- Page 1291 and 1292:
18.4 Solvent uses with exposure ris
- Page 1293 and 1294:
1268 Carlos M. Nu�ez ter or habit
- Page 1295 and 1296:
1270 Carlos M. Nu�ez CAS No. Chem
- Page 1297 and 1298:
1272 Carlos M. Nu�ez CAS No. Chem
- Page 1299 and 1300:
1274 Carlos M. Nu�ez CAS No. Chem
- Page 1301 and 1302:
1276 Carlos M. Nu�ez CAS No. Chem
- Page 1303 and 1304:
1278 Carlos M. Nu�ez CAS No. Chem
- Page 1305 and 1306:
1280 Carlos M. Nu�ez CAS No. Chem
- Page 1307 and 1308:
1282 Carlos M. Nu�ez tronic circu
- Page 1309 and 1310:
1284 Carlos M. Nu�ez EPA Region 6
- Page 1311 and 1312:
1286 Carlos M. Nu�ez i.e., entire
- Page 1313 and 1314:
1288 Carlos M. Nu�ez Table 19.6.
- Page 1315 and 1316:
1290 Carlos M. Nu�ez Schedule Sou
- Page 1317 and 1318:
1292 Carlos M. Nu�ez The CAA prov
- Page 1319 and 1320:
1294 Carlos M. Nu�ez CWA to estab
- Page 1321 and 1322:
1296 Carlos M. Nu�ez amended to i
- Page 1323 and 1324:
1298 Carlos M. Nu�ez Figure 19.5.
- Page 1325 and 1326:
1300 Carlos M. Nu�ez environmenta
- Page 1327 and 1328:
1302 Carlos M. Nu�ez For comparis
- Page 1329 and 1330:
1304 Carlos M. Nu�ez tives. Four
- Page 1331 and 1332:
1306 Carlos M. Nu�ez • Program
- Page 1333 and 1334:
1308 Carlos M. Nu�ez 31 Federal R
- Page 1335 and 1336:
1310 Carlos M. Nu�ez HSWA Hazardo
- Page 1337 and 1338:
1312 Tilman Hahn, Konrad Botzenhart
- Page 1339 and 1340:
20 Toxic Effects of Solvent Exposur
- Page 1341 and 1342:
20.1 Toxicokinetics, toxicodynamics
- Page 1343 and 1344:
20.1 Toxicokinetics, toxicodynamics
- Page 1345 and 1346:
20.1 Toxicokinetics, toxicodynamics
- Page 1347 and 1348:
20.1 Toxicokinetics, toxicodynamics
- Page 1349 and 1350:
20.1 Toxicokinetics, toxicodynamics
- Page 1351 and 1352:
20.2 Cognitive and psychosocial out
- Page 1353 and 1354:
20.2 Cognitive and psychosocial out
- Page 1355 and 1356:
20.2 Cognitive and psychosocial out
- Page 1357 and 1358:
20.3 Pregnancy outcome following so
- Page 1359 and 1360:
20.3 Pregnancy outcome following so
- Page 1361 and 1362:
20.3 Pregnancy outcome following so
- Page 1363 and 1364:
20.3 Pregnancy outcome following so
- Page 1365 and 1366:
20.3 Pregnancy outcome following so
- Page 1367 and 1368:
20.3 Pregnancy outcome following so
- Page 1369 and 1370:
20.3 Pregnancy outcome following so
- Page 1371 and 1372:
20.3 Pregnancy outcome following so
- Page 1373 and 1374:
20.3 Pregnancy outcome following so
- Page 1375 and 1376:
20.3 Pregnancy outcome following so
- Page 1377 and 1378:
20.3 Pregnancy outcome following so
- Page 1379 and 1380:
20.4 Industrial solvents and kidney
- Page 1381 and 1382:
20.4 Industrial solvents and kidney
- Page 1383 and 1384:
20.4 Industrial solvents and kidney
- Page 1385 and 1386:
20.4 Industrial solvents and kidney
- Page 1387 and 1388:
20.5 Lymphohematopoietic study of w
- Page 1389 and 1390:
20.5 Lymphohematopoietic study of w
- Page 1391 and 1392:
20.5 Lymphohematopoietic study of w
- Page 1393 and 1394:
20.5 Lymphohematopoietic study of w
- Page 1395 and 1396:
20.5 Lymphohematopoietic study of w
- Page 1397 and 1398:
20.5 Lymphohematopoietic study of w
- Page 1399 and 1400:
20.6 Chromosomal aberrations 1375 2
- Page 1401 and 1402:
20.6 Chromosomal aberrations 1377 p
- Page 1403 and 1404:
20.7 Hepatotoxicity 1379 8 Mitelman
- Page 1405 and 1406:
20.7 Hepatotoxicity 1381 to convert
- Page 1407 and 1408:
20.7 Hepatotoxicity 1383 Table 20.7
- Page 1409 and 1410:
20.7 Hepatotoxicity 1385 toxicity o
- Page 1411 and 1412:
20.7 Hepatotoxicity 1387 early pote
- Page 1413 and 1414:
20.7 Hepatotoxicity 1389 vents. It
- Page 1415 and 1416:
20.7 Hepatotoxicity 1391 19 Slater
- Page 1417 and 1418:
20.8 Solvents and the liver 1393 20
- Page 1419 and 1420:
20.8 Solvents and the liver 1395 Cu
- Page 1421 and 1422:
20.8 Solvents and the liver 1397 th
- Page 1423 and 1424:
20.8 Solvents and the liver 1399 cu
- Page 1425 and 1426:
20.8 Solvents and the liver 1401 20
- Page 1427 and 1428:
20.8 Solvents and the liver 1403 65
- Page 1429 and 1430:
20.9 Toxicity of environmental solv
- Page 1431 and 1432:
20.9 Toxicity of environmental solv
- Page 1433 and 1434:
20.9 Toxicity of environmental solv
- Page 1435 and 1436:
20.9 Toxicity of environmental solv
- Page 1437 and 1438:
20.9 Toxicity of environmental solv
- Page 1439 and 1440:
20.9 Toxicity of environmental solv
- Page 1441 and 1442:
20.9 Toxicity of environmental solv
- Page 1443 and 1444:
21 Substitution of Solvents by Safe
- Page 1445 and 1446:
21.1 Supercritical solvents 1421 So
- Page 1447 and 1448:
21.1 Supercritical solvents 1423 Fi
- Page 1449 and 1450:
21.1 Supercritical solvents 1425 Fi
- Page 1451 and 1452:
21.1 Supercritical solvents 1427 Fi
- Page 1453 and 1454:
21.1 Supercritical solvents 1429 K
- Page 1455 and 1456:
21.1 Supercritical solvents 1431 ai
- Page 1457 and 1458:
21.1 Supercritical solvents 1433 Th
- Page 1459 and 1460:
21.1 Supercritical solvents 1435 wh
- Page 1461 and 1462:
21.1 Supercritical solvents 1437 *
- Page 1463 and 1464:
21.1 Supercritical solvents 1439 In
- Page 1465 and 1466:
21.1 Supercritical solvents 1441 21
- Page 1467 and 1468:
21.1 Supercritical solvents 1443 Ta
- Page 1469 and 1470:
21.1 Supercritical solvents 1445 Re
- Page 1471 and 1472:
21.1 Supercritical solvents 1447 Re
- Page 1473 and 1474:
21.1 Supercritical solvents 1449 ta
- Page 1475 and 1476:
21.1 Supercritical solvents 1451 21
- Page 1477 and 1478:
21.1 Supercritical solvents 1453 Fi
- Page 1479 and 1480:
21.1 Supercritical solvents 1455 Fi
- Page 1481 and 1482:
21.1 Supercritical solvents 1457 13
- Page 1483 and 1484:
21.2 Ionic liquids 1459 85 M. Polia
- Page 1485 and 1486:
21.2 Ionic liquids 1461 be used. Th
- Page 1487 and 1488:
21.2 Ionic liquids 1463 Figure 21.2
- Page 1489 and 1490:
21.2 Ionic liquids 1465 Table 21.2.
- Page 1491 and 1492:
21.2 Ionic liquids 1467 been utiliz
- Page 1493 and 1494:
21.2 Ionic liquids 1469 One specifi
- Page 1495 and 1496:
21.2 Ionic liquids 1471 lustrates t
- Page 1497 and 1498:
21.2 Ionic liquids 1473 these alloy
- Page 1499 and 1500:
21.2 Ionic liquids 1475 ( ) ln = K
- Page 1501 and 1502:
21.2 Ionic liquids 1477 According t
- Page 1503 and 1504:
21.2 Ionic liquids 1479 Acidic melt
- Page 1505 and 1506:
21.2 Ionic liquids 1481 21 C.L. Hus
- Page 1507 and 1508:
21.2 Ionic liquids 1483 110 G.P. Li
- Page 1509 and 1510:
21.3 Oxide solubilities in ionic me
- Page 1511 and 1512:
21.3 Oxide solubilities in ionic me
- Page 1513 and 1514:
21.3 Oxide solubilities in ionic me
- Page 1515 and 1516:
21.3 Oxide solubilities in ionic me
- Page 1517 and 1518:
21.3 Oxide solubilities in ionic me
- Page 1519 and 1520:
21.3 Oxide solubilities in ionic me
- Page 1521 and 1522:
21.4 Alternative cleaning technolog
- Page 1523 and 1524:
21.4 Alternative cleaning technolog
- Page 1525 and 1526:
21.4 Alternative cleaning technolog
- Page 1527 and 1528:
21.4 Alternative cleaning technolog
- Page 1529 and 1530:
21.4 Alternative cleaning technolog
- Page 1531 and 1532:
1508 Klaus-Dirk Henning Application
- Page 1533 and 1534:
1510 Klaus-Dirk Henning 22.1.2.2 Ad
- Page 1535 and 1536:
1512 Klaus-Dirk Henning point the a
- Page 1537 and 1538:
1514 Klaus-Dirk Henning Figure 22.1
- Page 1539 and 1540:
1516 Klaus-Dirk Henning Figure 22.1
- Page 1541 and 1542:
1518 Klaus-Dirk Henning Table 22.1.
- Page 1543 and 1544:
1520 Klaus-Dirk Henning Figure 22.1
- Page 1545 and 1546:
1522 Klaus-Dirk Henning Regeneratio
- Page 1547 and 1548:
1524 Klaus-Dirk Henning • activit
- Page 1549 and 1550:
1526 Klaus-Dirk Henning adsorption
- Page 1551 and 1552:
1528 Klaus-Dirk Henning Figure 22.1
- Page 1553 and 1554:
1530 Klaus-Dirk Henning Figure 22.1
- Page 1555 and 1556:
1532 Klaus-Dirk Henning Figure 22.1
- Page 1557 and 1558:
1534 Klaus-Dirk Henning vent conden
- Page 1559 and 1560:
1536 Klaus-Dirk Henning Figure 22.1
- Page 1561 and 1562:
1538 Klaus-Dirk Henning Figure 22.1
- Page 1563 and 1564:
1540 Klaus-Dirk Henning Figure 22.1
- Page 1565 and 1566:
1542 Klaus-Dirk Henning 12 H. Krill
- Page 1567 and 1568:
1544 Isao Kimura Table 22.2.1. Appl
- Page 1569 and 1570:
1546 Isao Kimura Table 22.2.2. Typi
- Page 1571 and 1572:
1548 Isao Kimura 22.2.4 SOLVENT REC
- Page 1573 and 1574:
1550 Isao Kimura Figure 22.2.9. Flo
- Page 1575 and 1576:
1552 Isao Kimura • Difficult in d
- Page 1577 and 1578:
1554 Isao Kimura Figure 22.2.12. Fl
- Page 1579 and 1580:
1556 Denis Kargol Figure 22.3.1. So
- Page 1581 and 1582:
1558 Denis Kargol Figure 22.3.4. AS
- Page 1583 and 1584:
1560 K. A. Magrini, et al. and Olli
- Page 1585 and 1586:
1562 K. A. Magrini, et al. ysis of
- Page 1587 and 1588:
1564 K. A. Magrini, et al. Figure 2
- Page 1589 and 1590:
1566 K. A. Magrini, et al. On the l
- Page 1591 and 1592:
1568 K. A. Magrini, et al. ating te
- Page 1593 and 1594:
1570 K. A. Magrini, et al. Cummings
- Page 1595 and 1596:
1572 Hanadi S. Rifai, Charles J. Ne
- Page 1597 and 1598:
1574 Hanadi S. Rifai, Charles J. Ne
- Page 1599 and 1600:
1576 Hanadi S. Rifai, Charles J. Ne
- Page 1601 and 1602:
1578 Hanadi S. Rifai, Charles J. Ne
- Page 1603 and 1604:
1580 Hanadi S. Rifai, Charles J. Ne
- Page 1605 and 1606:
1582 Hanadi S. Rifai, Charles J. Ne
- Page 1607 and 1608:
1584 Hanadi S. Rifai, Charles J. Ne
- Page 1609 and 1610:
1586 Hanadi S. Rifai, Charles J. Ne
- Page 1611 and 1612:
1588 Hanadi S. Rifai, Charles J. Ne
- Page 1613 and 1614:
1590 Hanadi S. Rifai, Charles J. Ne
- Page 1615 and 1616:
1592 Hanadi S. Rifai, Charles J. Ne
- Page 1617 and 1618:
1594 Hanadi S. Rifai, Charles J. Ne
- Page 1619 and 1620:
1596 Hanadi S. Rifai, Charles J. Ne
- Page 1621 and 1622:
1598 Hanadi S. Rifai, Charles J. Ne
- Page 1623 and 1624:
1600 Hanadi S. Rifai, Charles J. Ne
- Page 1625 and 1626:
1602 Hanadi S. Rifai, Charles J. Ne
- Page 1627 and 1628:
1604 Hanadi S. Rifai, Charles J. Ne
- Page 1629 and 1630:
1606 Hanadi S. Rifai, Charles J. Ne
- Page 1631 and 1632:
1608 Hanadi S. Rifai, Charles J. Ne
- Page 1633 and 1634:
1610 Hanadi S. Rifai, Charles J. Ne
- Page 1635 and 1636:
1612 Hanadi S. Rifai, Charles J. Ne
- Page 1637 and 1638:
1614 Hanadi S. Rifai, Charles J. Ne
- Page 1639 and 1640:
1616 Hanadi S. Rifai, Charles J. Ne
- Page 1641 and 1642:
1618 Barry J. Spargo, James G. Muel
- Page 1643 and 1644:
1620 Barry J. Spargo, James G. Muel
- Page 1645 and 1646:
1622 Barry J. Spargo, James G. Muel
- Page 1647 and 1648:
1624 Barry J. Spargo, James G. Muel
- Page 1649 and 1650:
1626 Barry J. Spargo, James G. Muel
- Page 1651 and 1652:
1628 Barry J. Spargo, James G. Muel
- Page 1653 and 1654:
1630 Barry J. Spargo, James G. Muel
- Page 1655 and 1656:
1632 George Wypych number of 1 or e
- Page 1657 and 1658:
1634 George Wypych In addition to t
- Page 1659 and 1660:
1636 George Wypych d diameter of gr
- Page 1661 and 1662:
1638 George Wypych wax-containing c
- Page 1663 and 1664:
1640 George Wypych product of inven
- Page 1665 and 1666:
1642 George Wypych selection of sol
- Page 1667 and 1668:
1644 George Wypych fining processes
- Page 1669 and 1670:
1646 George Wypych requires several
- Page 1671 and 1672:
1648 George Wypych crease color str
- Page 1673 and 1674:
1650 George Wypych tion. The patent
- Page 1675 and 1676:
1652 George Wypych 75 M Solinas, T
- Page 1677 and 1678:
1658 Index anhydrous form 282 anili
- Page 1679 and 1680:
1660 Index 1-chlorooctane 826 chlor
- Page 1681 and 1682:
1662 Index term 750 dipole moment 1
- Page 1683 and 1684:
1664 Index Friedel-Crafts alkylatio
- Page 1685 and 1686:
1666 Index method 245 laser 689 lat
- Page 1687 and 1688:
1668 Index O octane 127,185 1-octan
- Page 1689 and 1690:
1670 Index Prandtl number 392 Praus
- Page 1691 and 1692:
1672 Index function 137 preferentia
- Page 1693 and 1694:
1674 Index change 350 time scale 33
Inappropriate
Loading...
Inappropriate
You have already flagged this document.
Thank you, for helping us keep this platform clean.
The editors will have a look at it as soon as possible.
Mail this publication
Loading...
Embed
Loading...
Delete template?
Are you sure you want to delete your template?
DOWNLOAD ePAPER
This ePaper is currently not available for download.
You can find similar magazines on this topic below under ‘Recommendations’.