Attention! Your ePaper is waiting for publication!
By publishing your document, the content will be optimally indexed by Google via AI and sorted into the right category for over 500 million ePaper readers on YUMPU.
This will ensure high visibility and many readers!
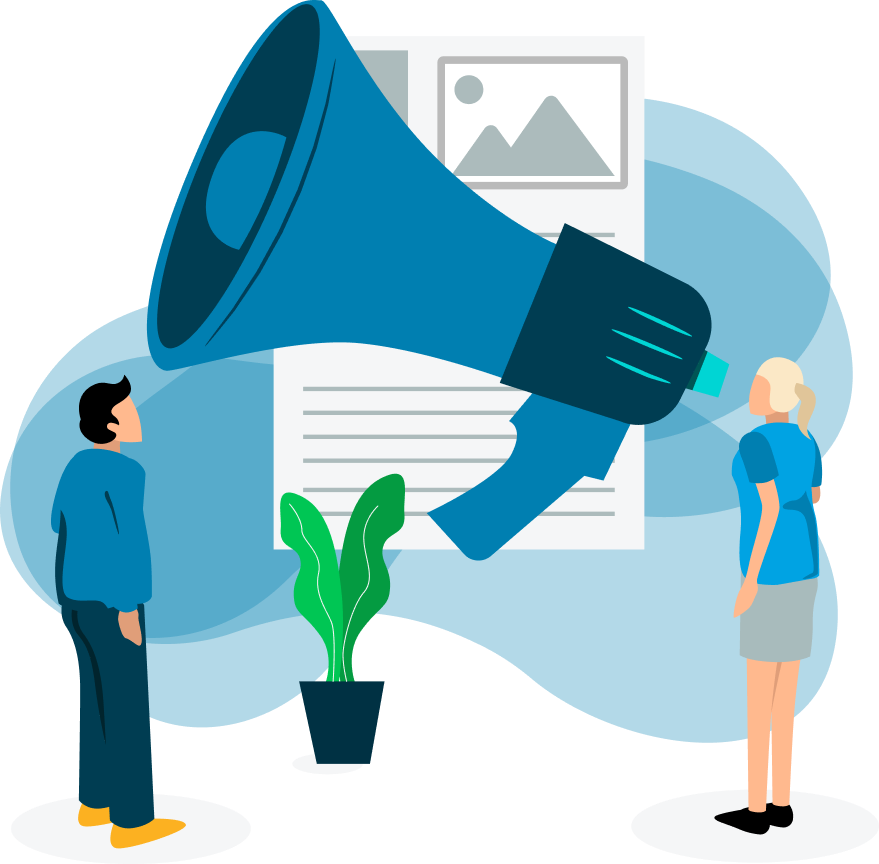
Your ePaper is now published and live on YUMPU!
You can find your publication here:
Share your interactive ePaper on all platforms and on your website with our embed function
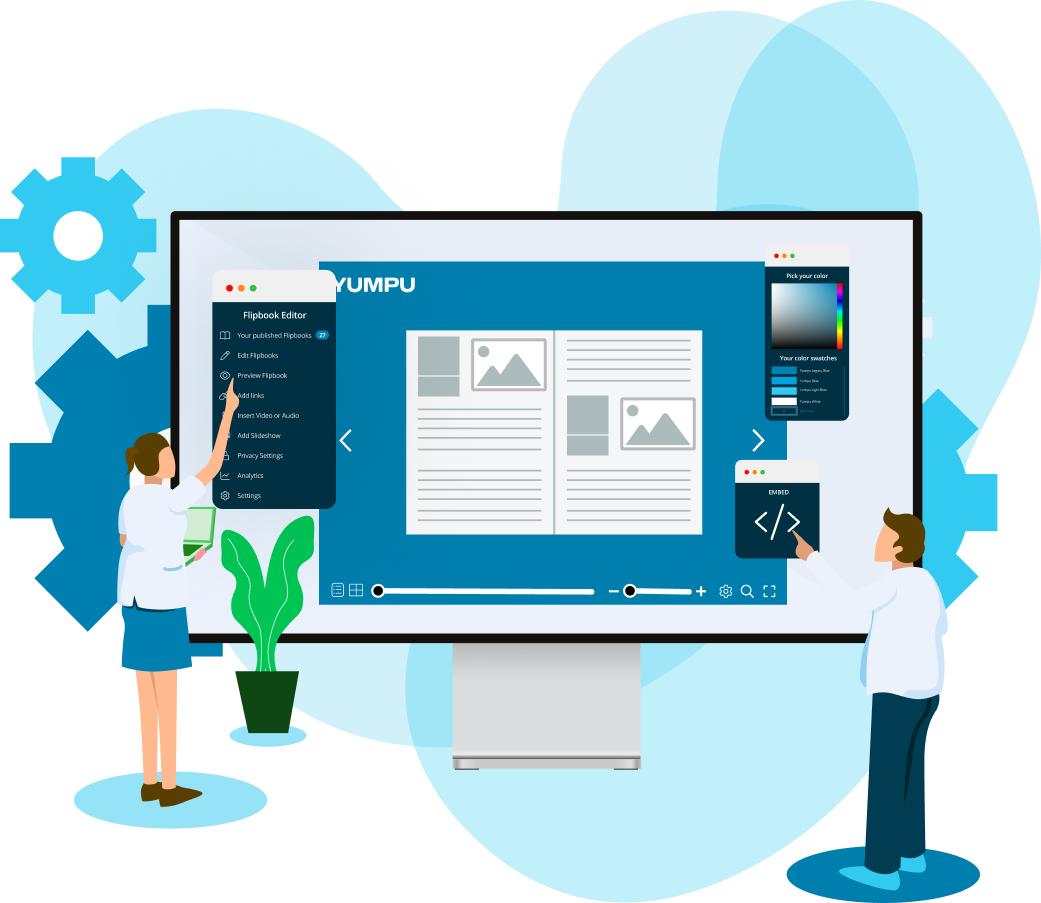
Practical Guige to Free Energy Devices
eBook 3000 pages! author: Patrick J. Kelly "This eBook contains most of what I have learned about this subject after researching it for a number of years. I am not trying to sell you anything, nor am I trying to convince you of anything. When I started looking into this subject, there was very little useful information and any that was around was buried deep in incomprehensible patents and documents. My purpose here is to make it easier for you to locate and understand some of the relevant material now available. What you believe is up to yourself and is none of my business. Let me stress that almost all of the devices discussed in the following pages, are devices which I have not personally built and tested. It would take several lifetimes to do that and it would not be in any way a practical option. Consequently, although I believe everything said is fully accurate and correct, you should treat everything as being “hearsay” or opinion. Some time ago, it was commonly believed that the world was flat and rested on the backs of four elephants and that when earthquakes shook the ground, it was the elephants getting restless. If you want to believe that, you are fully at liberty to do so, however, you can count me out as I don’t believe that. " THE MATERIAL PRESENTED IS FOR INFORMATION PURPOSES ONLY. SHOULD YOU DECIDE TO PERFORM EXPERIMENTS OR CONSTRUCT ANY DEVICE, YOU DO SO WHOLLY ON YOUR OWN RESPONSIBILITY -- NEITHER THE COMPANY HOSTING THIS WEB SITE, NOR THE SITE DESIGNER ARE IN ANY WAY RESPONSIBLE FOR YOUR ACTIONS OR ANY RESULTING LOSS OR DAMAGE OF ANY DESCRIPTION, SHOULD ANY OCCUR AS A RESULT OF WHAT YOU DO.
eBook 3000 pages!
author: Patrick J. Kelly
"This eBook contains most of what I have learned about this subject after researching it for a number of years. I am not trying to sell you anything, nor am I trying to convince you of anything. When I started looking into this subject, there was very little useful information and any that was around was buried deep in incomprehensible patents and documents. My purpose here is to make it easier for you to locate and understand some of the relevant material now available. What you believe is up to yourself and is none of my business. Let me stress that almost all of the devices discussed in the following pages, are devices which I have not personally built and tested. It would take several lifetimes to do that and it would not be in any way a practical option. Consequently, although I believe everything said is fully accurate and correct, you should treat everything as being “hearsay” or opinion.
Some time ago, it was commonly believed that the world was flat and rested on the backs of four elephants and that when earthquakes shook the ground, it was the elephants getting restless. If you want to believe that, you are fully at liberty to do so, however, you can count me out as I don’t believe that. "
THE MATERIAL PRESENTED IS FOR INFORMATION PURPOSES ONLY. SHOULD YOU DECIDE TO PERFORM EXPERIMENTS OR CONSTRUCT ANY DEVICE, YOU DO SO WHOLLY ON YOUR OWN RESPONSIBILITY -- NEITHER THE COMPANY HOSTING THIS WEB SITE, NOR THE SITE DESIGNER ARE IN ANY WAY RESPONSIBLE FOR YOUR ACTIONS OR ANY RESULTING LOSS OR DAMAGE OF ANY DESCRIPTION, SHOULD ANY OCCUR AS A RESULT OF WHAT YOU DO.
- No tags were found...
You also want an ePaper? Increase the reach of your titles
YUMPU automatically turns print PDFs into web optimized ePapers that Google loves.
We need <strong>to</strong> pass a mild steel pipe through the plate in the centre of the square, and we are not going <strong>to</strong> put in any<br />
additional work on the hub plate until we have the pipe in place and its welding is confirmed <strong>to</strong> be accurate. The<br />
pipe is needed <strong>to</strong> give the thin hub plate stability when rotating around the 50 mm diameter axle shaft, and so, it<br />
should be at least 100 mm (4-inches) long when installed. There is a mild steel pipe with 80.78 mm inner<br />
diameter and an outer diameter of 88.9 mm and a wall thickness of 4.06 mm. That gives a clearance of just 0.39<br />
mm all around the bearing and allows the bearing <strong>to</strong> be tack welded directly <strong>to</strong> the pipe which has a robust wall<br />
thickness.<br />
Cut a 300 mm length of the pipe and position it carefully in the centre of the square marked in the middle of the<br />
hub plate. Draw carefully around it <strong>to</strong> show the size and position where the pipe needs <strong>to</strong> go. We now have the<br />
difficulty of getting the pipe through the hub plate. With a powerful plasma cutter that would be no problem and<br />
the circular cut could be made quite easily, but it is definitely <strong>to</strong>o expensive <strong>to</strong> buy one for just that one cut,<br />
although hiring one and an air compressor for a morning might be an option.<br />
With the most simple <strong>to</strong>ols you could cut out the largest possible square in the centre of the circle and then use a<br />
round file (and a lot of effort) <strong>to</strong> cut back the remaining metal <strong>to</strong> make the required circle. A more crude method is<br />
<strong>to</strong> just cut out a square and settle for welding the pipe at the four points where it <strong>to</strong>uches the hub plate.<br />
Remember that the moment the weld is made on one side of the hub plate, the other side of the hub plate needs<br />
<strong>to</strong> be welded immediately and both allowed <strong>to</strong> cool as slowly as possible <strong>to</strong> avoid heat shrinkage pulling the pipe<br />
out of its alignment with the hub plate. Remember that the hub plate will be hot enough <strong>to</strong> burn you even if the<br />
weld only <strong>to</strong>ok a split second <strong>to</strong> make, so take care. In other words, if the pipe is vertical, then (almost)<br />
simultaneous welds need <strong>to</strong> be made on the <strong>to</strong>p of the hub plate and on the underside of the hub plate. The<br />
thicker the steel, the easier it is <strong>to</strong> weld without problems and the pipe is straightforward <strong>to</strong> weld with its 4 mm<br />
thickness. It takes a great deal of skill <strong>to</strong> weld steel sheet of 1 mm thickness without tearing a hole in the sheet,<br />
but thankfully, that is not something which you need <strong>to</strong> do with this design.<br />
Before welding, we need <strong>to</strong> stand the pipe piece exactly vertical <strong>to</strong> the hub plate, with 50 mm projecting beyond<br />
the hub plate. This can be done easily with four permanent magnet units intended specifically for this job. They<br />
are very powerful and look like this:<br />
These attach strongly <strong>to</strong> both the pipe and the hub plate and with one every 90 degrees around the axle, it is held<br />
very securely in place, leaving plenty of space for the initial welds. In early 2016, a set of four of these right-angle<br />
magnets costs £10 in the UK.<br />
Having tack-welded the pipe carefully and quickly on both sides, using welds only 6 mm or so long, and having<br />
waited for those welds <strong>to</strong> cool down fully, make two additional tack welds at 180 degrees <strong>to</strong> the first two, and then<br />
two more pairs so as <strong>to</strong> have a weld every 90 degrees around the pipe. This leaves you with 50 mm of pipe<br />
20 - 11
When cutting or grinding always wear protective goggles <strong>to</strong> make sure that you don’t get a metal fragment in your eye – eyes are not readily replaceable !! If you do get a small steel fragment in your eye, remember that steel is highly magnetic and so a magnet may help in getting the fragment out with the minimum of damage, however, it is much, much easier <strong>to</strong> wear goggles and not have the problem in the first place. For this genera<strong>to</strong>r, we start by making the hub. While a circular shape can be produced using simple <strong>to</strong>ols, there is actually no need and so we can just use straight edges which are much easier <strong>to</strong> produce. So, for this, we cut a square of metal 350 mm along each face: This is an important structural component and so it would be good if the metal was 10 mm thick or even thicker. We need <strong>to</strong> construct an arrangement where the 2-metre diameter flywheel is supported on two 16010 bearings which have an inner diameter of 50 mm, an outer diameter of 80 mm and a thickness of 10 mm. For this, a length of mild steel pipe needs <strong>to</strong> be inserted through the hub plate and welded in position at exactly right angles <strong>to</strong> the hub plate. But, for the moment, back <strong>to</strong> our square piece of steel which we intend <strong>to</strong> become the hub plate of our main flywheel. Draw diagonals from the corners <strong>to</strong> establish where the centre of the square is, then mark a 90 mm square centred exactly on that centre point, and draw a vertical and horizontal line, like this: Measure 175 mm out along the diagonals and mark each of those four points. Then, connect those points <strong>to</strong> make an even octagon: 20 - 10
We need <strong>to</strong> pass a mild steel pipe through the plate in the centre of the square, and we are not going <strong>to</strong> put in any additional work on the hub plate until we have the pipe in place and its welding is confirmed <strong>to</strong> be accurate. The pipe is needed <strong>to</strong> give the thin hub plate stability when rotating around the 50 mm diameter axle shaft, and so, it should be at least 100 mm (4-inches) long when installed. There is a mild steel pipe with 80.78 mm inner diameter and an outer diameter of 88.9 mm and a wall thickness of 4.06 mm. That gives a clearance of just 0.39 mm all around the bearing and allows the bearing <strong>to</strong> be tack welded directly <strong>to</strong> the pipe which has a robust wall thickness. Cut a 300 mm length of the pipe and position it carefully in the centre of the square marked in the middle of the hub plate. Draw carefully around it <strong>to</strong> show the size and position where the pipe needs <strong>to</strong> go. We now have the difficulty of getting the pipe through the hub plate. With a powerful plasma cutter that would be no problem and the circular cut could be made quite easily, but it is definitely <strong>to</strong>o expensive <strong>to</strong> buy one for just that one cut, although hiring one and an air compressor for a morning might be an option. With the most simple <strong>to</strong>ols you could cut out the largest possible square in the centre of the circle and then use a round file (and a lot of effort) <strong>to</strong> cut back the remaining metal <strong>to</strong> make the required circle. A more crude method is <strong>to</strong> just cut out a square and settle for welding the pipe at the four points where it <strong>to</strong>uches the hub plate. Remember that the moment the weld is made on one side of the hub plate, the other side of the hub plate needs <strong>to</strong> be welded immediately and both allowed <strong>to</strong> cool as slowly as possible <strong>to</strong> avoid heat shrinkage pulling the pipe out of its alignment with the hub plate. Remember that the hub plate will be hot enough <strong>to</strong> burn you even if the weld only <strong>to</strong>ok a split second <strong>to</strong> make, so take care. In other words, if the pipe is vertical, then (almost) simultaneous welds need <strong>to</strong> be made on the <strong>to</strong>p of the hub plate and on the underside of the hub plate. The thicker the steel, the easier it is <strong>to</strong> weld without problems and the pipe is straightforward <strong>to</strong> weld with its 4 mm thickness. It takes a great deal of skill <strong>to</strong> weld steel sheet of 1 mm thickness without tearing a hole in the sheet, but thankfully, that is not something which you need <strong>to</strong> do with this design. Before welding, we need <strong>to</strong> stand the pipe piece exactly vertical <strong>to</strong> the hub plate, with 50 mm projecting beyond the hub plate. This can be done easily with four permanent magnet units intended specifically for this job. They are very powerful and look like this: These attach strongly <strong>to</strong> both the pipe and the hub plate and with one every 90 degrees around the axle, it is held very securely in place, leaving plenty of space for the initial welds. In early 2016, a set of four of these right-angle magnets costs £10 in the UK. Having tack-welded the pipe carefully and quickly on both sides, using welds only 6 mm or so long, and having waited for those welds <strong>to</strong> cool down fully, make two additional tack welds at 180 degrees <strong>to</strong> the first two, and then two more pairs so as <strong>to</strong> have a weld every 90 degrees around the pipe. This leaves you with 50 mm of pipe 20 - 11
- Page 1 and 2:
Author: Patrick J. Kelly Version: 3
- Page 3 and 4:
to get the results described, that
- Page 5 and 6:
The 1982 patent of Heinrich Kunel .
- Page 7 and 8:
Chapter 9: Passive Systems Hans Coh
- Page 9 and 10:
Jesse McQueen . . . . . . . . . . .
- Page 11 and 12:
Spiro Spiros’ COP>1 electrolyser
- Page 13 and 14:
At this point in time - the early y
- Page 15 and 16:
For example, consider a crystal set
- Page 17 and 18:
The actual situation is, that we ar
- Page 19 and 20:
The science taught in schools, coll
- Page 21 and 22:
kinds for sale ready-made. We have
- Page 23 and 24:
Today, we know that these things ar
- Page 25 and 26:
Conventional science says that it c
- Page 27 and 28:
The final shaft drives a standard e
- Page 29 and 30:
efrigerator, for years on end. Conv
- Page 31 and 32:
The electrical pulses to the screen
- Page 33 and 34:
Moray's demonstrations were highly
- Page 35 and 36:
The Colman / Seddon-Gillespie 70-ye
- Page 37 and 38:
Conclusion: The term "Free-Energy"
- Page 39 and 40:
Dan Cook’s self-powered motionles
- Page 41 and 42:
This is the Climachill Ltd. PAC12H
- Page 43 and 44:
A Practical Guide to Free-Energy De
- Page 45 and 46:
There is a patent on the motor but
- Page 47 and 48:
Here, the same shielding idea is ut
- Page 49 and 50:
Or there could be four coils: The c
- Page 51 and 52:
The magnet arrangement is shown her
- Page 53 and 54:
This is a patent which is definitel
- Page 55 and 56:
The Jines Permanent Magnet Motor. J
- Page 57 and 58:
Figures 2 and 3 show the position o
- Page 59 and 60:
permanent magnet motor also uses th
- Page 61 and 62:
Shown here is the situation when on
- Page 63 and 64:
It should be remembered that the ti
- Page 65 and 66:
Connecting several coils "in series
- Page 67 and 68:
As this allows the speed to be cont
- Page 69 and 70:
Video presentations on this style o
- Page 71 and 72:
This style of magnet arrangement (N
- Page 73 and 74:
As there is no commentary with the
- Page 75 and 76:
With Dietmar’s design using angle
- Page 77 and 78:
They have not disclosed all of the
- Page 79 and 80:
A square of wood can then be screwe
- Page 81 and 82:
The output shaft spins around one a
- Page 83 and 84:
Fig.2a is an oblique view of the in
- Page 85 and 86:
Fig.6 is a perspective view of the
- Page 87 and 88:
Fig.10 shows the positions of magne
- Page 89 and 90:
Fig.12b shows the arrangement of th
- Page 91 and 92:
The outer stator 3 is composed of t
- Page 93 and 94:
with its end face aligned with the
- Page 95 and 96:
Fig.17a is a schematic representati
- Page 97 and 98:
magnets in all seven series 701 to
- Page 99 and 100:
moves magnets of the opposite polar
- Page 101 and 102:
Each magnet is attracted to the met
- Page 103 and 104:
includes at least one drive magnet
- Page 105 and 106:
Fig.4 is a schematic diagram of one
- Page 107 and 108:
Fig.4 and Fig.5 demonstrate the ori
- Page 109 and 110:
thereby reducing the number transmi
- Page 111 and 112:
In an embodiment of the magnetic dr
- Page 113 and 114:
FIG. 1 is a diagrammatic perspectiv
- Page 115 and 116:
FIG. 5 is a timing diagram showing
- Page 117 and 118:
FIGS. 6A-6H are further timing diag
- Page 119 and 120:
FIG. 10A is a cross-sectional view
- Page 121 and 122:
FIGS. 12A and 12B are enlarged pers
- Page 123 and 124:
1 - 81
- Page 125 and 126:
FIG. 15 is a diagrammatic perspecti
- Page 127 and 128:
FIG. 19 is a perspective view showi
- Page 129 and 130:
material may be used to fabricate t
- Page 131 and 132:
It should be noted that the power z
- Page 133 and 134:
een determined to be quite short, a
- Page 135 and 136:
figure shows the magnet carrier rel
- Page 137 and 138:
Fig.6F shows the magnet carriers 4,
- Page 139 and 140:
Turning now to Figs.8-12B, the magn
- Page 141 and 142:
With continuing reference to Figs.8
- Page 143 and 144:
Although each of the magnetic drive
- Page 145 and 146:
Fig.20 shows another magnetic drive
- Page 147 and 148:
Further, a good deal of experimenta
- Page 149 and 150:
ecause of the tapering of the coppe
- Page 151 and 152:
The diagrams presented by Robert sh
- Page 153 and 154:
Robert Adams has used this construc
- Page 155 and 156:
magnetic materials, each atom has m
- Page 157 and 158:
These outmoded methods have gone on
- Page 159 and 160:
Note on battery tests: I have done
- Page 161 and 162:
2 - 16
- Page 163 and 164:
2 - 18
- Page 165 and 166:
2 - 20
- Page 167 and 168:
2 - 22
- Page 169 and 170:
The unique rotor, briefly described
- Page 171 and 172:
with the mechanical energy that we
- Page 173 and 174:
Those of us interested in the 'free
- Page 175 and 176:
20 0.812 21 0.813 1.5 3.5 21 0.723
- Page 177 and 178:
http://www.totallyamped.net/adams/i
- Page 179 and 180:
The stator preferably comprises a p
- Page 181 and 182:
Fig.4A shows a schematic view of a
- Page 183 and 184:
Fig.7 shows a graphical representat
- Page 185 and 186:
Fig.11 shows a further graphical re
- Page 187 and 188:
A description of the operation of t
- Page 189 and 190:
Although current can be applied to
- Page 191 and 192:
c. When using permanent magnets whi
- Page 193 and 194:
When the permanent magnet is at 0°
- Page 195 and 196:
Therefore if the induced magnetic f
- Page 197 and 198:
coupled to the surface of the rotor
- Page 199 and 200:
Fig.1 depicts a longitudinal cross-
- Page 201 and 202:
Fig.3 depicts a centre cross sectio
- Page 203 and 204:
Fig.5 and Fig.6 depict the interact
- Page 205 and 206:
Fig.7 depicts a longitudinal cross-
- Page 207 and 208:
In Fig.9, the portion of the magnet
- Page 209 and 210:
and recharge a battery bank in the
- Page 211 and 212:
This device is also capable of driv
- Page 213 and 214:
third. This non-linear relationship
- Page 215 and 216:
Fig.4 and Fig.5 illustrate diagramm
- Page 217 and 218:
shaft 103, extend over arcs of appr
- Page 219 and 220:
Fig.3 shows a generator 300 which i
- Page 221 and 222:
In this motor, a series of electrom
- Page 223 and 224:
The housing is divided into three s
- Page 225 and 226:
and having a common point 25. It is
- Page 227 and 228:
Fig.5, a diagrammatic view of a var
- Page 229 and 230:
Fig.1 shows diagrammatically, a mac
- Page 231 and 232:
The gain “g” in power per unit
- Page 233 and 234:
In Fig.7, 110 and 112 designate the
- Page 235 and 236:
The objective is to tune the motor
- Page 237 and 238:
It is suggested that the jumpering
- Page 239 and 240:
T. J. Chorister in America has used
- Page 241 and 242:
You will notice that when the open
- Page 243 and 244:
Doug Konzen has been developing thi
- Page 245 and 246:
The heavy rotor provides some flywh
- Page 247 and 248:
establishment routinely dismiss an
- Page 249 and 250:
Mr Tseung remarks that the large wh
- Page 251 and 252:
Here, just two of the cross timbers
- Page 253 and 254:
With this arrangement, Art states t
- Page 255 and 256:
Here, one pair of brushes is at the
- Page 257 and 258:
The final wire turn goes down throu
- Page 259 and 260:
And as before, the commutator secto
- Page 261 and 262:
Here, the designation “R/S” sta
- Page 263 and 264:
disconnected the motor (the total r
- Page 265 and 266:
A Practical Guide to Free-Energy De
- Page 267 and 268:
common sense but it makes it clear
- Page 269 and 270:
A variation of this arrangement is
- Page 271 and 272:
I wrote an article on this subject,
- Page 273 and 274:
However, all the known transformers
- Page 275 and 276:
Fig.2 shows another embodiment of t
- Page 277 and 278:
Fig.8 shows a stylized dependence o
- Page 279 and 280:
A transformer in accordance with th
- Page 281 and 282:
At a low load resistance (equal to
- Page 283 and 284:
the DC resistance can be minimised
- Page 285 and 286:
Figure 2. C-I and E-I resonant setu
- Page 287 and 288:
available from www.goldwave.com. I
- Page 289 and 290:
other and there are induced magneti
- Page 291 and 292:
The sliding brass contact or “bru
- Page 293 and 294:
understand clearly that the current
- Page 295 and 296:
The blue coil has the power input a
- Page 297 and 298:
efficient working system. The load
- Page 299 and 300:
This is the actual drawing from the
- Page 301 and 302:
(10), which converts the alternatin
- Page 303 and 304:
Figure 4 - shows a third embodiment
- Page 305 and 306:
Fig.2, shows another embodiment of
- Page 307 and 308:
patent application No. BR1020120008
- Page 309 and 310:
facing the north pole of the magnet
- Page 311 and 312:
Fig.2 - is a representation of Fara
- Page 313 and 314:
Fig.7 - is a representation of an e
- Page 315 and 316:
In electron-traps which have numero
- Page 317 and 318:
AWG #4 2.5 turn windings are wound
- Page 319 and 320:
Here are some pictures of Clarence
- Page 321 and 322:
Components used were: Toroids: ----
- Page 323 and 324:
However, the situation changes cons
- Page 325 and 326:
A 110V supply is supposed to swing
- Page 327 and 328:
Lorrie also extended his developmen
- Page 329 and 330:
You will notice that these circuits
- Page 331 and 332:
This original patent application is
- Page 333 and 334:
effect in the primary magnetic path
- Page 335 and 336:
of switch 110 is additive to the ma
- Page 337 and 338:
Fig.7A depicts a preferred construc
- Page 339 and 340:
If this interruption of the flux fl
- Page 341 and 342:
The linear energy generator shown i
- Page 343 and 344:
pulse of the induction flux 5 induc
- Page 345 and 346:
generators which use the transforma
- Page 347 and 348:
This invention relates to a dynamo
- Page 349 and 350:
Fig.3 represents how a flux in the
- Page 351 and 352:
Fig.8 is a fourth embodiment of the
- Page 353 and 354:
The first core 2 and the second cor
- Page 355 and 356:
Next, the power generation efficien
- Page 357 and 358:
magnetic path can be formed in two
- Page 359 and 360:
That is, as indicated in Fig.9, the
- Page 361 and 362:
Stephan states that he has built th
- Page 363 and 364:
This shows clearly that the open en
- Page 365 and 366:
The working pictures of Floyd’s p
- Page 367 and 368:
Frequency generally affected resist
- Page 369 and 370:
Table 1 3 - 105
- Page 371 and 372:
0.72 Mev this which corresponds to
- Page 373 and 374:
The Devices of Don Smith. One free-
- Page 375 and 376:
This circuitry confirms what Don sa
- Page 377 and 378:
The induced electric field exists i
- Page 379 and 380:
When we connect these two plates by
- Page 381 and 382:
direction of rotation to be CCW (Fi
- Page 383 and 384:
This is why we need a high-voltage
- Page 385 and 386:
The above explanation describes the
- Page 387 and 388:
epresent my thoughts and understand
- Page 389 and 390:
The above explanation will help to
- Page 391 and 392:
When the capacitor discharges acros
- Page 393 and 394:
Physically (Fig.23) the electromagn
- Page 395 and 396:
F be the available voltage since th
- Page 397 and 398:
The two yellow capacitors seen abov
- Page 399 and 400:
positions of the magnetic and elect
- Page 401 and 402:
The best combination between the le
- Page 403 and 404:
When converting the reactive electr
- Page 405 and 406:
alternating current. Thousands of T
- Page 407 and 408:
old video, and I recommend everybod
- Page 409 and 410:
general-purpose lighting instead of
- Page 411 and 412:
Video at http://www.youtube.com/wat
- Page 413 and 414:
3 - 149
- Page 415 and 416:
3 - 151
- Page 417 and 418:
An earlier entry on the Chinese for
- Page 419 and 420:
3 - 155
- Page 421 and 422:
In my circuit, the frequency used i
- Page 423 and 424:
Nick has had very impressive result
- Page 425 and 426:
capacitor before being used to driv
- Page 427 and 428:
can be connected together in parall
- Page 429 and 430:
used to do work. The oscillator cir
- Page 431 and 432:
Fig.6 is a section view of a full l
- Page 433 and 434:
Fig.4 is a view of a full-length el
- Page 435 and 436:
inductance, in a receiver, between
- Page 437 and 438:
appear to be not fluctuating at all
- Page 439 and 440:
Accordingly, Fig.2 (which includes
- Page 441 and 442:
and the information then replicated
- Page 443 and 444:
It is actually quite difficult to s
- Page 445 and 446:
The device being displayed is a Tes
- Page 447 and 448:
There is some additional informatio
- Page 449 and 450:
12. Lawrence Tseung has shown how a
- Page 451 and 452:
While this circuit looks like somet
- Page 453 and 454:
A FET has a gate capacitance of abo
- Page 455 and 456:
In the ‘UFOpolitics’ circuit, i
- Page 457 and 458:
My lowest frequency was 133Hz (I ne
- Page 459 and 460:
It is also taught by the prior art,
- Page 461 and 462:
Fig.5 is another alternative arrang
- Page 463 and 464:
Fig.10 is an illustration of an alt
- Page 465 and 466:
Fig.5 shows a coil arrangement 49,
- Page 467 and 468:
The magnetic particle accelerator 1
- Page 469 and 470:
Russ, in his discussion, points out
- Page 471 and 472:
Fig.1 shows the general layout of t
- Page 473 and 474:
Fig.4 above, is an electrical diagr
- Page 475 and 476:
Fig.7 above, illustrates the option
- Page 477 and 478:
The wire end marked “A” will be
- Page 479 and 480:
This shows how completely the (red)
- Page 481 and 482:
Video: http://www.youtube.com/watch
- Page 483 and 484:
If the rotor spins well, then it wo
- Page 485 and 486:
Jacob Byzehr’s Analysis. In 1998,
- Page 487 and 488:
However, the various types of gener
- Page 489 and 490:
The electric drive motor (1) provid
- Page 491 and 492:
Here, the additional output can be
- Page 493 and 494:
The Centrifugal Energy Amplificatio
- Page 495 and 496:
The 25th September 1989 patent appl
- Page 497 and 498:
2. The speed of the wheel turning i
- Page 499 and 500:
https://www.alibaba.com/product-det
- Page 501 and 502:
Presumably, the arm is curved to av
- Page 503 and 504:
The way that the chain manages to p
- Page 505 and 506:
This is because the larger lever ar
- Page 507 and 508:
Admittedly, the deflector pieces wo
- Page 509 and 510:
The question, of course is, will th
- Page 511 and 512:
greater mass of beam A. If an addit
- Page 513 and 514:
likely to be a geared one so that t
- Page 515 and 516:
However, if the linked weights were
- Page 517 and 518:
With this arrangement, the outer we
- Page 519 and 520:
It is pointed out that the lower gu
- Page 521 and 522:
system does not rely on wind, weath
- Page 523 and 524:
Fig.3 shows one version of the firs
- Page 525 and 526:
Fig.9 shows an alternative embodime
- Page 527 and 528:
A Simple Buoyancy Power Generator A
- Page 529 and 530:
Fig.2, is a cross-sectional concept
- Page 531 and 532:
Fig.4, is a perspective conceptual
- Page 533 and 534:
this arrangement is that the tank i
- Page 535 and 536:
again on the ascending side of the
- Page 537 and 538:
The idea is that the liquid on the
- Page 539 and 540:
COP=1200, each household would rece
- Page 541 and 542:
When the system is switched off, th
- Page 543 and 544:
There are, of course, many differen
- Page 545 and 546:
The motor needs to be linked to the
- Page 547 and 548:
For this style of construction, fou
- Page 549 and 550:
Two timber strips 1350 mm long, are
- Page 551 and 552:
It should be explained that, with t
- Page 553 and 554:
This is the position when at rest.
- Page 555 and 556:
A Practical Guide to Free-Energy De
- Page 557 and 558:
current is the same as the earth-ge
- Page 559 and 560:
the local environment, and in this
- Page 561 and 562:
It is recommended that this simple-
- Page 563 and 564:
in the drawing. I strongly recommen
- Page 565 and 566:
and that keeps their operation shor
- Page 567 and 568:
While the above diagram shows each
- Page 569 and 570:
The overall circuit for the opto sw
- Page 571 and 572:
Tests on one of the pure white unit
- Page 573 and 574:
Each base resistor has an output li
- Page 575 and 576:
Or using current day symbols: 5 - 2
- Page 577 and 578:
This current flow through primary w
- Page 579 and 580:
When a bell is struck just once, it
- Page 581 and 582:
pairs from each other, keeping a co
- Page 583 and 584:
No one part of an induction coil ma
- Page 585 and 586:
This insertion of paper increases t
- Page 587 and 588:
This circuit shows the circuit conn
- Page 589 and 590:
desired inductance, and finally, th
- Page 591 and 592:
necessary to get it charged up to 1
- Page 593 and 594:
cyclic connection of the capacitors
- Page 595 and 596:
Fig.2 shows a practical circuit in
- Page 597 and 598:
Fig.6 shows the electrical diagram
- Page 599 and 600:
etween both pairs of batteries. At
- Page 601 and 602:
Fig.6 shows the connection of a dir
- Page 603 and 604:
Walter Ford’s High-powered Crysta
- Page 605 and 606:
oadcast band - say, 1500 kHz - and
- Page 607 and 608:
operating. He runs the circuit driv
- Page 609 and 610:
Quite good lighting can be had from
- Page 611 and 612:
As the LED array lights are essenti
- Page 613 and 614:
The arrangement is for the inner wi
- Page 615 and 616:
With proper modifications this circ
- Page 617 and 618:
When the circuit has been built as
- Page 619 and 620:
With the appropriate modifications
- Page 621 and 622:
We come now to circuits designed by
- Page 623 and 624:
A Suggestion This is an arrangement
- Page 625 and 626:
4. Make sure that the flash is not
- Page 627 and 628:
7. The two switches which form the
- Page 629 and 630:
This “Super Joule Ringer 3.0” c
- Page 631 and 632:
A video of this unit being demonstr
- Page 633 and 634:
Radiant Energy, when converted to e
- Page 635 and 636:
With a pulse duration of 1 microsec
- Page 637 and 638:
Energy stored, multiplied by the cy
- Page 639 and 640:
After careful consideration and man
- Page 641 and 642:
In Joseph Cater’s book “The Awe
- Page 643 and 644:
As it seems to me that there are ma
- Page 645 and 646:
An attempted translation of the pat
- Page 647 and 648:
1. The output voltage does not chan
- Page 649 and 650:
ocaf.org are working with Rosemary'
- Page 651 and 652:
Dr Oleg Gritskevitch’s 1.5 Megawa
- Page 653 and 654:
the dynamo does not accumulate any
- Page 655 and 656:
titanate in the Armenian dynamo was
- Page 657 and 658:
The battery connects at the back, u
- Page 659 and 660:
produce a pulse which keeps the rot
- Page 661 and 662:
Ron Pugh’s Battery Charger. John
- Page 663 and 664:
The magnets embedded in the outer e
- Page 665 and 666:
The three coils have a total of fif
- Page 667 and 668:
6 - 12
- Page 669 and 670:
When a magnet passes the coil conta
- Page 671 and 672:
Although the circuit diagram shows
- Page 673 and 674:
e increased by raising the input vo
- Page 675 and 676:
As you can see, the trick is to pla
- Page 677 and 678:
attery and the charging battery. Fo
- Page 679 and 680:
charging battery and keep doing thi
- Page 681 and 682:
The build used has three electromag
- Page 683 and 684:
not matter either, which way round
- Page 685 and 686:
The Self-Charging Motor. A video at
- Page 687 and 688:
If building a circuit with a solder
- Page 689 and 690:
Alexkor’s Self-Charging Circuit.
- Page 691 and 692:
If the coil is wound on say, a 1.25
- Page 693 and 694:
The coil is tiny, bi-filar wound on
- Page 695 and 696:
If you use the bolt section of one
- Page 697 and 698:
Here, the size of the voltage pulse
- Page 699 and 700:
The simple circuit shown here was u
- Page 701 and 702:
The motor is demonstrated when set
- Page 703 and 704:
This motor is shown running on capa
- Page 705 and 706:
Popp, their evidence is that batter
- Page 707 and 708:
When pin 3 of the 555 goes low, res
- Page 709 and 710:
The 3-Kilowatt Earth Battery This b
- Page 711 and 712:
Magnesium gives excellent results,
- Page 713 and 714:
Einstein, the reality is that it wa
- Page 715 and 716:
Again, it is essential that the wir
- Page 717 and 718:
Please remember that it is Bob Boyc
- Page 719 and 720:
Consequently, it is distinctly poss
- Page 721 and 722:
This is a slightly unusual circuit
- Page 723 and 724:
With an arrangement like that it is
- Page 725 and 726:
It seems probable that this device
- Page 727 and 728:
Fig.1 shows the simplest form, in w
- Page 729 and 730:
It is clear from what has been stat
- Page 731 and 732:
The length of the thin wire coil in
- Page 733 and 734:
Now, consider this circuit as descr
- Page 735 and 736:
have a good aerial connected throug
- Page 737 and 738:
Using two of these boards, Dragan i
- Page 739 and 740:
Thomas developed various versions o
- Page 741 and 742:
The tube of Fig.16 above, uses a di
- Page 743 and 744:
Batteries with their positive and n
- Page 745 and 746:
At last they decided to go up Emigr
- Page 747 and 748:
With the 60 watt lamp and the two c
- Page 749 and 750:
accompanied by corresponding change
- Page 751 and 752:
of these energies. Every part and p
- Page 753 and 754:
When a certain voltage is reached,
- Page 755 and 756:
Herman starts by illustrating how w
- Page 757 and 758:
West direction. However, replicatio
- Page 759 and 760:
In one implementation of the invent
- Page 761 and 762:
Diodes: D1, D2, D3 and D4 - Germani
- Page 763 and 764:
information purposes only” and th
- Page 765 and 766:
This invention converts inertial im
- Page 767 and 768:
SUMMARY OF THE INVENTION The Harmon
- Page 769 and 770:
DETAILED DESCRIPTION OF A PREFERRED
- Page 771 and 772:
What is said in this patent applica
- Page 773 and 774:
But for the Earth's magnetic field,
- Page 775 and 776:
Fig.2 is another diagram further il
- Page 777 and 778:
otor 11 by the charging electrode 1
- Page 779 and 780:
Another object of the present inven
- Page 781 and 782:
Fig.5 is a circuit diagram incorpor
- Page 783 and 784:
Fig.9 is a vertical sectional view
- Page 785 and 786:
extending bars 36 is supported in a
- Page 787 and 788:
In Fig.5, the stator bars are diagr
- Page 789 and 790:
In the system shown in Fig.7, an in
- Page 791 and 792:
In general, the basic electrical sy
- Page 793 and 794:
Initially, at start-up, both of the
- Page 795 and 796:
A Practical Guide to Free-Energy De
- Page 797 and 798:
The people who don’t want self-po
- Page 799 and 800:
First, you have an ordinary air eng
- Page 801 and 802:
This patent shows how the practical
- Page 803 and 804:
Summary of the Invention: These and
- Page 805 and 806:
Fig.3 is a frontal view of the impe
- Page 807 and 808:
Fig.7 is a perspective view of a se
- Page 809 and 810:
The front housing section 32 is a h
- Page 811 and 812:
transition duct 96 is believed to r
- Page 813 and 814:
slightly curved. The blades gradual
- Page 815 and 816:
With respect to the application of
- Page 817 and 818:
This results in the air temperature
- Page 819 and 820:
The operating pressure produced by
- Page 821 and 822:
Josef never managed to get his engi
- Page 823 and 824:
petroleum products to operate. Mich
- Page 825 and 826:
This invention relates generally to
- Page 827 and 828:
working fluid opening which may be
- Page 829 and 830:
7. The heat pump of claim 6 wherein
- Page 831 and 832:
Fig.3 is a cross section and Fig.4
- Page 833 and 834:
In Fig.3, a rotor for a unit using
- Page 835 and 836:
US Patent 3,931,713 13th January 19
- Page 837 and 838:
Fig.3 is a cross section of another
- Page 839 and 840:
Fig.2 shows an end view of the unit
- Page 841 and 842:
The vanes of the rotors may be made
- Page 843 and 844:
thinking of it as a fuel-less or se
- Page 845 and 846:
Proprietary liquids, specifically c
- Page 847 and 848:
Additional warm air to augment air
- Page 849 and 850:
And the schematic diagram is: One e
- Page 851 and 852:
Thomas is by no means the first per
- Page 853 and 854:
more than a minute or so. If there
- Page 855 and 856:
According to this invention, the bl
- Page 857 and 858:
The frame of the pyramid is not the
- Page 859 and 860:
The very fine filter-grade quartz s
- Page 861 and 862:
The capacitor is positioned inside
- Page 863 and 864:
Thomas’ website which is in Germa
- Page 865 and 866:
frame pyramids. This area is wide o
- Page 867 and 868:
James invites you to run this test
- Page 869 and 870:
(2) Placing an insulated coil on th
- Page 871 and 872:
ut in time you will see the tremend
- Page 873 and 874:
used within its glass walls. Pest-f
- Page 875 and 876:
to eat it, but if I was going to pr
- Page 877 and 878:
had the same sensations of coldness
- Page 879 and 880:
which are much closer to those of t
- Page 881 and 882:
Photographs 1 and 2 show two differ
- Page 883 and 884:
destructive phenomena, you destroy
- Page 885 and 886:
The Cell itself is made up with the
- Page 887 and 888:
Seven or eight stainless steel cone
- Page 889 and 890:
part of the diagram. Cut another wa
- Page 891 and 892:
This arrangement looks more complic
- Page 893 and 894:
aligned. The spacers will be more e
- Page 895 and 896:
mode was being used. The surprising
- Page 897 and 898:
operates by breaking water down int
- Page 899 and 900:
In the installation shown above, yo
- Page 901 and 902:
If tack-welded cylinders have to be
- Page 903 and 904:
As stated earlier, the first 5 mile
- Page 905 and 906:
airtight! Go and do something else.
- Page 907 and 908:
engine starts to ping. When the tim
- Page 909 and 910:
It should be clearly understood tha
- Page 911 and 912:
Comments from an expert in July 201
- Page 913 and 914:
To be sure that the second and thir
- Page 915 and 916:
The claims made for this coil are q
- Page 917 and 918:
encouraging you personally to try t
- Page 919 and 920:
idea of the universe which you have
- Page 921 and 922:
A: There are several workshops wher
- Page 923 and 924:
A Practical Guide to Free-Energy De
- Page 925 and 926:
the Space Shuttle into space! If yo
- Page 927 and 928:
circuit and each power socket circu
- Page 929 and 930:
The plate shapes shown above are ar
- Page 931 and 932:
Any of these designs can be 6-cell
- Page 933 and 934:
and so has to be accepted as an ove
- Page 935 and 936:
A good source for general component
- Page 937 and 938:
To deal with this, a one-way valve
- Page 939 and 940:
A point which might not be immediat
- Page 941 and 942:
The method which Zach uses is somew
- Page 943 and 944:
It is always difficult to make a go
- Page 945 and 946:
If, in spite of all precautions, yo
- Page 947 and 948:
shock-wave when it is ignited so th
- Page 949 and 950:
Caution: This electrolyser is not a
- Page 951 and 952:
The items marked with a blue dot fo
- Page 953 and 954:
The six electrolyser cells and the
- Page 955 and 956:
When used with rainwater from a bar
- Page 957 and 958:
The arrangement with three cells co
- Page 959 and 960:
It is available from ship’s chand
- Page 961 and 962:
This second layer is wound in exact
- Page 963 and 964:
who is outstanding in this field is
- Page 965 and 966:
The technique of DC pulsing require
- Page 967 and 968:
The bolts tapped into the inner tub
- Page 969 and 970:
These arms get two bends in them in
- Page 971 and 972:
In this rather unusual circuit, the
- Page 973 and 974:
Circuit operation: The main part of
- Page 975 and 976:
second. The larger the capacitor, t
- Page 977 and 978:
Here, the 555 chip output voltage i
- Page 979 and 980:
The underside of the strip-board (w
- Page 981 and 982:
Component Quantity Description Comm
- Page 983 and 984:
conventional electricity, and it ha
- Page 985 and 986:
The outer pipes are drilled and tap
- Page 987 and 988:
method is by powering the cell up f
- Page 989 and 990:
Dr. Cramton says: “I would like p
- Page 991 and 992:
Dave Lawton’s Auto-Tune Circuit.
- Page 993 and 994:
Because of these things, the calcul
- Page 995 and 996:
Here, they have opted to feed the H
- Page 997 and 998:
Diesel has the same structure but w
- Page 999 and 1000:
we definitely do not want that to h
- Page 1001 and 1002:
Making the HHO gas When the generat
- Page 1003 and 1004:
Boyce would need 400 watts without
- Page 1005 and 1006:
• Powder Coated Finish • Light
- Page 1007 and 1008:
The ball is held in place by the sp
- Page 1009 and 1010:
The pipes, backing plate, pressure-
- Page 1011 and 1012:
for a year. The objective is to del
- Page 1013 and 1014:
5. Next comes a bit of arithmetic.
- Page 1015 and 1016:
The copper pipe is then heated with
- Page 1017 and 1018:
The water is then treated by insert
- Page 1019 and 1020:
greater pressure on the piston duri
- Page 1021 and 1022:
The first part of David Quirey’s
- Page 1023 and 1024:
Let me stress that this is just an
- Page 1025 and 1026:
and while, not surprisingly, I have
- Page 1027 and 1028:
Developed in conjunction with the E
- Page 1029 and 1030:
electrical generator. The engine ra
- Page 1031 and 1032:
The sole explanation of the explosi
- Page 1033 and 1034:
This turbine creates a spinning air
- Page 1035 and 1036:
Ted created the egg-shaped part of
- Page 1037 and 1038:
degrees. With it’s 350 cubic inch
- Page 1039 and 1040:
Roger Maynard’s Water Vapour Inje
- Page 1041 and 1042:
“Fuelsavers” Streamlining Fins.
- Page 1043 and 1044:
I started out in 1976 when the firs
- Page 1045 and 1046:
properly, saving the government a l
- Page 1047 and 1048:
educed accordingly. If the Gen III
- Page 1049 and 1050:
flow. This is a useful energy gain
- Page 1051 and 1052:
This is an unusual voltage-doubler
- Page 1053 and 1054:
While on the other hand, if negativ
- Page 1055 and 1056:
describes many possible application
- Page 1057 and 1058:
Suartt and Gourley realised that th
- Page 1059 and 1060:
produced by this process is likely
- Page 1061 and 1062:
Fig.4 illustrates graphs showing th
- Page 1063 and 1064:
which do not provoke electrolysis o
- Page 1065 and 1066:
SG Gas, the tank was decompressed a
- Page 1067 and 1068:
Fig.5 shows a typical absorption ov
- Page 1069 and 1070:
Biological Properties Transport, De
- Page 1071 and 1072:
This reaction changes water from a
- Page 1073 and 1074:
With this unit, air is sucked out o
- Page 1075 and 1076:
etween these plates, these craters
- Page 1077 and 1078:
In the years leading up to 1970, ex
- Page 1079 and 1080:
These sanctions which were initiate
- Page 1081 and 1082:
spotlight, and yet, he is carrying
- Page 1083 and 1084:
A Practical Guide to Free-Energy De
- Page 1085 and 1086:
does not appear to be any reason wh
- Page 1087 and 1088:
Brief Description of the Drawings F
- Page 1089 and 1090:
aether phase-lock cannot force the
- Page 1091 and 1092:
Referring to Fig.2, the inductors 3
- Page 1093 and 1094:
combination of the two capacitor-in
- Page 1095 and 1096:
power by tapping energy from space.
- Page 1097 and 1098:
to the innermost electrodes. This m
- Page 1099 and 1100:
state” exhibiting the attributes
- Page 1101 and 1102:
The force of the Zero-Point Energy
- Page 1103 and 1104:
If you find the concept of producin
- Page 1105 and 1106:
ook, also later in this chapter, po
- Page 1107 and 1108:
(B) (i) The orthodox view of a heli
- Page 1109 and 1110:
Electromagnetic output is a functio
- Page 1111 and 1112:
When you place a magnet on the door
- Page 1113 and 1114:
11 - 31
- Page 1115 and 1116:
The outer magnets in the diagram ab
- Page 1117 and 1118:
He also suggests that monopole grav
- Page 1119 and 1120:
Here, there is no net electrical or
- Page 1121 and 1122:
Ferrite is a better material for th
- Page 1123 and 1124:
Joseph has been granted a patent an
- Page 1125 and 1126:
The next interesting point is that
- Page 1127 and 1128:
Joseph then went on to consider the
- Page 1129 and 1130:
Maxwell says that there is a vast s
- Page 1131 and 1132:
In any given instant of time, the a
- Page 1133 and 1134:
magnet of some 600 pounds in weight
- Page 1135 and 1136:
Davis makes the following observati
- Page 1137 and 1138:
coil should be wound in the same di
- Page 1139 and 1140:
Edmund says: Each output coils’ h
- Page 1141 and 1142:
use of any heating fuel. This next
- Page 1143 and 1144:
1009908 November 1911 Lafore 111594
- Page 1145 and 1146:
pressure of the gas being entrained
- Page 1147 and 1148:
turbines and pumps and so are not d
- Page 1149 and 1150:
Fig.1 shows a heat transfer system
- Page 1151 and 1152:
DETAILED DESCRIPTION Referring to F
- Page 1153 and 1154:
When operating, a voltage is applie
- Page 1155 and 1156:
US 3,065,935, Duberry/Frost/Earl US
- Page 1157 and 1158:
This small selection of forty-six p
- Page 1159 and 1160:
In addition, Nieper established the
- Page 1161 and 1162:
Means of Operation The device is st
- Page 1163 and 1164:
In late 2001, I wrote a magazine ar
- Page 1165 and 1166:
of matter and is nothing more than
- Page 1167 and 1168:
Hypothetically, is certainly the in
- Page 1169 and 1170:
7. Nieper, Hans A., Ph.D., 1985, Co
- Page 1171 and 1172:
Summary: In accordance with the pre
- Page 1173 and 1174:
Fig.5A and Fig.5B are schematic par
- Page 1175 and 1176:
Referring now to Figs 2, 3 and 4 in
- Page 1177 and 1178:
According to the embodiment of the
- Page 1179 and 1180:
invention does not perform any subs
- Page 1181 and 1182:
I’m a geologist. And the one thin
- Page 1183 and 1184:
one of them took the bacteria, deve
- Page 1185 and 1186:
Bob Beck’s Electronic Pulser. The
- Page 1187 and 1188:
There is a parts list on page 4 tha
- Page 1189 and 1190:
This is a theory: about 30% of the
- Page 1191 and 1192:
Finance: Money only has value when
- Page 1193 and 1194:
Moon, a seismic detector left on th
- Page 1195 and 1196:
of a particle is inversely proporti
- Page 1197 and 1198:
It now becomes evident, why a mass
- Page 1199 and 1200:
intensity of these zones, determine
- Page 1201 and 1202:
The leading part of the gravity rad
- Page 1203 and 1204:
light has to be of high intensity.
- Page 1205 and 1206:
freezing point, the molecular activ
- Page 1207 and 1208:
apparently a factor in it’s perfo
- Page 1209 and 1210:
the surface area is sufficient to a
- Page 1211 and 1212:
least squares. Conventional statist
- Page 1213 and 1214:
the insulation and stop at the surf
- Page 1215 and 1216:
together and the resulting ethers e
- Page 1217 and 1218:
any other type of radiation such as
- Page 1219 and 1220:
an orgone accumulator. ------------
- Page 1221 and 1222:
There are several different types o
- Page 1223 and 1224:
Examples: Red, Red, Red: 2 2 00 ohm
- Page 1225 and 1226:
As before, the colour coding is exa
- Page 1227 and 1228:
This determination of the voltage l
- Page 1229 and 1230:
If a bulb is used instead of R2, th
- Page 1231 and 1232:
at about 8 Volts. We can use Ohm’
- Page 1233 and 1234:
Then the LED gets connected to the
- Page 1235 and 1236:
transistor. A gain of 200 means tha
- Page 1237 and 1238:
Here, an additional transistor (‘
- Page 1239 and 1240:
The design covered above is not the
- Page 1241 and 1242:
With this circuit, two ordinary dio
- Page 1243 and 1244:
This is not an FET transistor and s
- Page 1245 and 1246:
functioning. If the Power Supply Un
- Page 1247 and 1248:
devices, immune to shock and vibrat
- Page 1249 and 1250:
The main difference being that when
- Page 1251 and 1252:
The strength of the magnetic field
- Page 1253 and 1254:
Instead, if you connect the 10 Volt
- Page 1255 and 1256:
This produces a much better result
- Page 1257 and 1258:
Multivibrators: The Bistable. The n
- Page 1259 and 1260:
2. The press-button switch is opera
- Page 1261 and 1262:
Here, The input impedance has been
- Page 1263 and 1264:
Here, a slow-running astable is sub
- Page 1265 and 1266:
time. Small fingers and good eyesig
- Page 1267 and 1268:
shown on the right. There is now a
- Page 1269 and 1270:
in this voltage level since it is b
- Page 1271 and 1272:
Astable Frequencies 100 470 1K 4.7K
- Page 1273 and 1274:
http://www.talkingelectronics.com/p
- Page 1275 and 1276:
ohm resistor in the output line whi
- Page 1277 and 1278:
So, what value do we need for “R2
- Page 1279 and 1280:
Bob Beck’s design calls for the L
- Page 1281 and 1282:
The two 18V zener diodes drop off 1
- Page 1283 and 1284:
To avoid shock liability, use batte
- Page 1285 and 1286:
Here, the gain is set by the ratio
- Page 1287 and 1288:
This circuit is set up as evening f
- Page 1289 and 1290:
There are three connections to the
- Page 1291 and 1292:
If pin 14 is provided with the outp
- Page 1293 and 1294:
In this example, the sequence is st
- Page 1295 and 1296:
single chip, and which is called a
- Page 1297 and 1298:
The last line "goto Main" tells the
- Page 1299 and 1300:
Capacitors. We have avoided mention
- Page 1301 and 1302:
The time has come for a serious war
- Page 1303 and 1304:
DC we would multiply them together
- Page 1305 and 1306:
These have a coil of wire wound aro
- Page 1307 and 1308:
For the moment, we will ignore the
- Page 1309 and 1310:
Relay switching is not so critical
- Page 1311 and 1312:
The first strand of the coil starts
- Page 1313 and 1314:
The decoupling is to provide the 55
- Page 1315 and 1316:
It can also be useful to have a ver
- Page 1317 and 1318:
So, when you are deciding what mult
- Page 1319 and 1320:
Resistor ‘VR1’ is padded with t
- Page 1321 and 1322:
output meter display to zero when t
- Page 1323 and 1324:
attery to an electrical circuit, th
- Page 1325 and 1326:
The major physical principles invol
- Page 1327 and 1328:
Another possibility is that the jar
- Page 1329 and 1330:
However, when this is done, the bru
- Page 1331 and 1332:
The circuit shown here is broken by
- Page 1333 and 1334:
and build a release field. Then the
- Page 1335 and 1336:
No hydrogen is consumed. No additio
- Page 1337 and 1338:
alone more than 100%. This system w
- Page 1339 and 1340:
completely to show that there was n
- Page 1341 and 1342:
Numbers used on the schematic: 1- A
- Page 1343 and 1344:
BACKGROUND OF THE INVENTION Electri
- Page 1345 and 1346:
power the electric motor. The secon
- Page 1347 and 1348:
un using air and hydrogen as the fu
- Page 1349 and 1350:
nuts tightened on a 10 mm (3/8”)
- Page 1351 and 1352:
The inner nuts are manoeuvred on in
- Page 1353 and 1354:
just the relay current to be handle
- Page 1355 and 1356:
The bolt is kept just clear of the
- Page 1357 and 1358:
4. How do you determine the amount
- Page 1359 and 1360:
Electrical Generation: The cell wil
- Page 1361 and 1362:
From another user: Hi, thanks for t
- Page 1363 and 1364:
These two cells have been in use in
- Page 1365 and 1366:
urning status should you choose to
- Page 1367 and 1368:
There are also many problems with t
- Page 1369 and 1370:
This looks as if the pressure tank
- Page 1371 and 1372:
The objective is to get two stainle
- Page 1373 and 1374:
If a standard laminated iron yoke i
- Page 1375 and 1376:
paranoid reaction. Perhaps, I would
- Page 1377 and 1378:
Closed Systems and Open Systems If
- Page 1379 and 1380:
an open system, which brings us to
- Page 1381 and 1382:
captures all of the magnetic field
- Page 1383 and 1384:
Because the MEG is an open system,
- Page 1385 and 1386:
Note that the M1 coil is reversed.
- Page 1387 and 1388:
A Practical Guide to Free-Energy De
- Page 1389 and 1390:
Wood of any type, branches, sticks,
- Page 1391 and 1392:
http://www.woodgas.net/index.html -
- Page 1393 and 1394:
A system like this needs extreme ca
- Page 1395 and 1396:
Mr Kim also shows a burner intended
- Page 1397 and 1398:
Sterling’s web site is definitely
- Page 1399 and 1400:
The “heat exchanger” is a radia
- Page 1401 and 1402:
Peter Davey’s AC Heater. During W
- Page 1403 and 1404:
http://www.overunity.com/index.php?
- Page 1405 and 1406:
14 - 19
- Page 1407 and 1408:
I changed the connections inside my
- Page 1409 and 1410:
This view shows two important featu
- Page 1411 and 1412:
a good angle when flowing through t
- Page 1413 and 1414:
existing methods. The parabolic coo
- Page 1415 and 1416:
Construction Steps Cut a Half-circl
- Page 1417 and 1418:
The easiest way to do this is to pu
- Page 1419 and 1420:
usual, to trap the heat. The suspen
- Page 1421 and 1422:
Cooking times are approximate. Incr
- Page 1423 and 1424:
spread this technology is to encour
- Page 1425 and 1426:
on opposite ends of the funnel is f
- Page 1427 and 1428:
The power is found in Watts. A powe
- Page 1429 and 1430:
cookers provide a sustainable techn
- Page 1431 and 1432:
How can one readily determine if th
- Page 1433 and 1434:
IDEXX Laboratories, Inc. makes the
- Page 1435 and 1436:
pulled back to let the condensation
- Page 1437 and 1438:
Mark the underside of the flaps of
- Page 1439 and 1440:
This effect is very noticeable on f
- Page 1441 and 1442:
By applying these same methods on a
- Page 1443 and 1444:
14 - 57
- Page 1445 and 1446:
It is, of course, essential for the
- Page 1447 and 1448:
ATMOSPHERIC WATER SUPPLY APPARATUS
- Page 1449 and 1450:
Fig.3 is a sectional view taken sub
- Page 1451 and 1452:
Referring now to figures 2, 3, 4 an
- Page 1453 and 1454:
Another system is using a large Fre
- Page 1455 and 1456:
5. Antibiotics have no impact whats
- Page 1457 and 1458:
For a decade, Musk’s startup call
- Page 1459 and 1460:
Arthur Bentley’s Water Pump. The
- Page 1461 and 1462:
The performance of a Ram Pump is im
- Page 1463 and 1464:
small flies, by hanging polythene b
- Page 1465 and 1466:
This has the very considerable adva
- Page 1467 and 1468:
Also, a two-part article on Solar c
- Page 1469 and 1470:
terminates in a distributor head 31
- Page 1471 and 1472:
do your own checking as designs cha
- Page 1473 and 1474:
Rated at up to 3 Amp-Hour capacity,
- Page 1475 and 1476:
The only moving component in this s
- Page 1477 and 1478:
------------------- Without knowing
- Page 1479 and 1480:
Here, the extra switch marked “BO
- Page 1481 and 1482:
If there are not wires already atta
- Page 1483 and 1484:
10. It is much easier to work on th
- Page 1485 and 1486:
14. The final connections which nee
- Page 1487 and 1488:
17. Connect a voltmeter across the
- Page 1489 and 1490:
The same voltage reading should be
- Page 1491 and 1492:
This is making a connection between
- Page 1493 and 1494:
---------------------- There are ot
- Page 1495 and 1496:
While these particular units have j
- Page 1497 and 1498:
With fully charged batteries switch
- Page 1499 and 1500:
360 Degree Lighting for Africa The
- Page 1501 and 1502:
If ordinary 10-battery holders are
- Page 1503 and 1504:
echarging mobile phones. It should
- Page 1505 and 1506:
These metres show more than 100-wat
- Page 1507 and 1508:
The pads are kept wet by droplets o
- Page 1509 and 1510:
This one at https://www.youtube.com
- Page 1511 and 1512:
The objective is to make a home whi
- Page 1513 and 1514:
The overall design is set up for co
- Page 1515 and 1516:
The constructional details can be f
- Page 1517 and 1518:
When the wall is finished off and t
- Page 1519 and 1520:
The important thing to remember abo
- Page 1521 and 1522:
There was one group of landowners w
- Page 1523 and 1524:
If you feel that these things are a
- Page 1525 and 1526:
you at all unless you consent to be
- Page 1527 and 1528:
Do you feel that you are obliged to
- Page 1529 and 1530:
purchased was transported to the sh
- Page 1531 and 1532:
the enemy of the United States Gove
- Page 1533 and 1534:
loans at interest, and that was the
- Page 1535 and 1536:
of the Federal Reserve, there was n
- Page 1537 and 1538:
world trade system and to build up
- Page 1539 and 1540:
have enough gold to cover the outst
- Page 1541 and 1542:
But understand this above all else,
- Page 1543 and 1544:
Iran 1953: The precedent for econom
- Page 1545 and 1546:
Panama 1981: Omar Tarrijas Presiden
- Page 1547 and 1548:
doesn’t. And in the case of Iraq,
- Page 1549 and 1550:
Inspector of Schools, has recently
- Page 1551 and 1552:
every useful forum with a combinati
- Page 1553 and 1554:
anything about keeping to a speed l
- Page 1555 and 1556:
delivered to them. The financial in
- Page 1557 and 1558:
above mentioned papers and readily
- Page 1559 and 1560:
Patent. Under no circumstances hear
- Page 1561 and 1562:
and appurtenances… we perform and
- Page 1563 and 1564:
went - to the Crown Temple. This sh
- Page 1565 and 1566:
WMAQ - Chicago WCAU - Philadelphia
- Page 1567 and 1568:
Sweden and wife of King Gustav. Lou
- Page 1569 and 1570:
Silent weapon technology has evolve
- Page 1571 and 1572:
sources of natural and social energ
- Page 1573 and 1574:
association of consumer preferences
- Page 1575 and 1576:
(a few examples will be given.) Cha
- Page 1577 and 1578:
Economic Shock Testing In recent ti
- Page 1579 and 1580:
Liabilities: (1) Creditors (2) Enem
- Page 1581 and 1582:
(10) Controls manufacturing. (11) C
- Page 1583 and 1584:
If this rise of the lower classes c
- Page 1585 and 1586:
oken down into categories by intell
- Page 1587 and 1588:
Further, there are no penalties in
- Page 1589 and 1590:
And showing the flattening of the g
- Page 1591 and 1592:
Here, the poorest billion people wa
- Page 1593 and 1594:
This states that it is a crime to p
- Page 1595 and 1596:
A Practical Guide to Free-Energy De
- Page 1597 and 1598:
It is not necessary to "go for brok
- Page 1599 and 1600:
Another device which is not hard to
- Page 1601 and 1602:
as that, but perhaps one of say, th
- Page 1603 and 1604:
Devices Which are the Easiest to Bu
- Page 1605 and 1606:
whether or not there are any genera
- Page 1607 and 1608:
Ron Classen has replicated this des
- Page 1609 and 1610:
devices have to be rated as some of
- Page 1611 and 1612:
This design appeals to most people
- Page 1613 and 1614:
Thomas Henry Moray’s Aerial Syste
- Page 1615 and 1616:
Do you have any values for Peter Lo
- Page 1617 and 1618:
so I suggest that you begin with an
- Page 1619 and 1620:
electrolyzer following your plans a
- Page 1621 and 1622:
which he used to power an electrica
- Page 1623 and 1624:
You state in the literature that th
- Page 1625 and 1626:
"How 2 Fix To create a power source
- Page 1627 and 1628:
My frequency reads 35.4 KHz or 3540
- Page 1629 and 1630:
wire length ratio between L1 and L2
- Page 1631 and 1632:
So, if you let your high-frequency
- Page 1633 and 1634:
Question: I may have missed any dis
- Page 1635 and 1636:
Question: Always been a fan of your
- Page 1637 and 1638:
You will notice that each of these
- Page 1639 and 1640:
This circuit will have all three tr
- Page 1641 and 1642:
Chapter 17: An Easy-Build Generator
- Page 1643 and 1644:
Each plank is supplied with a facto
- Page 1645 and 1646:
It is suggested that the rotor is d
- Page 1647 and 1648:
A really major advantage of this ty
- Page 1649 and 1650:
This arrangement has sixteen coils,
- Page 1651 and 1652: drill blocks the view from vertical
- Page 1653 and 1654: We now want to cut out the rotor (b
- Page 1655 and 1656: Leave 30 mm below the lowest plank
- Page 1657 and 1658: These saw sets normally have a saw
- Page 1659 and 1660: eaches that of the second highest v
- Page 1661 and 1662: This arrangement allows complete fl
- Page 1663 and 1664: This transistor is popular and is a
- Page 1665 and 1666: You will notice that there is a dio
- Page 1667 and 1668: If you prefer not to make coil spoo
- Page 1669 and 1670: A Practical Guide to Free-Energy De
- Page 1671 and 1672: Fig. 4. Explanation of the principl
- Page 1673 and 1674: Fig. 7. The simplest manifestation
- Page 1675 and 1676: Fig. 10. Using asymmetrical electro
- Page 1677 and 1678: Fig.14 Voltage distribution on the
- Page 1679 and 1680: Fig. 18 Schematic from the Donald S
- Page 1681 and 1682: Chapter 19: Building A Motor / Gene
- Page 1683 and 1684: John’s design starts with a DC mo
- Page 1685 and 1686: John says that he tunes his design
- Page 1687 and 1688: If you are careful to get the centr
- Page 1689 and 1690: Cut out the marked lines and work t
- Page 1691 and 1692: to the battery to recharge it. Inst
- Page 1693 and 1694: A Practical Guide to Free-Energy De
- Page 1695 and 1696: The performance is most impressive
- Page 1697 and 1698: Driven by an AC mains motor, once r
- Page 1699 and 1700: With this “stick welder” the si
- Page 1701: For this construction, each of the
- Page 1705 and 1706: The spokes are made with 50 mm x 50
- Page 1707 and 1708: There are a few additions to be mad
- Page 1709 and 1710: All right, that is the first way to
- Page 1711 and 1712: No matter what tool is used, don’
- Page 1713 and 1714: It is not at all easy to take a wel
- Page 1715 and 1716: This diagram shows only one drive m
- Page 1717 and 1718: In the position shown, the Generato
- Page 1719 and 1720: ase of the transistor, causing it t
- Page 1721 and 1722: of plastic pipe which prevents the
- Page 1723 and 1724: where the direction of twist revers
- Page 1725 and 1726: This arrangement allows the value o
- Page 1727 and 1728: The load could be buffered from the
- Page 1729 and 1730: The idea here is that the reels of
- Page 1731 and 1732: An American contributor who prefers
- Page 1733 and 1734: commercially and which is covered i
- Page 1735 and 1736: shelf and a narrow shelf. The sides
- Page 1737 and 1738: 22-8
- Page 1739 and 1740: If you intend to paint the housing,
- Page 1741 and 1742: The ‘Variac’ variable mains tra
- Page 1743 and 1744: This has the effect of overcoming a
- Page 1745 and 1746: The NST unit is readily available a
- Page 1747 and 1748: We now come to the items which we n
- Page 1749 and 1750: However, the overall arrangement sh
- Page 1751 and 1752: This board is called type “B” a
- Page 1753 and 1754:
One detail to be mentioned is the t
- Page 1755 and 1756:
The idea is to cut a groove or chan
- Page 1757 and 1758:
to the two ends of my first number
- Page 1759 and 1760:
the setting up of your machine. Fai
- Page 1761 and 1762:
Socket Surge Protector Strip Plug E
- Page 1763 and 1764:
Appendix TABLE OF WIRE SIZES: The w
- Page 1765 and 1766:
Briefly stated, the present inventi
- Page 1767 and 1768:
shaped magnet having a rear side an
- Page 1769 and 1770:
Fig.2 is a schematic plan view of a
- Page 1771 and 1772:
Fig.7A is a schematic plan view of
- Page 1773 and 1774:
Fig.9 is a schematic perspective vi
- Page 1775 and 1776:
Fig.12 is an end elevational view o
- Page 1777 and 1778:
Fig.15B is an end elevational view
- Page 1779 and 1780:
Fig.19 is an elevational end view o
- Page 1781 and 1782:
further aspect of the rotor 12, as
- Page 1783 and 1784:
the U-shaped magnets 20 having subs
- Page 1785 and 1786:
Referring now to Fig.1B, Fig.2 and
- Page 1787 and 1788:
an axis 16 of the rotor 12. The mot
- Page 1789 and 1790:
Preferably, the surface 64 of the s
- Page 1791 and 1792:
A - 29
- Page 1793 and 1794:
Referring now to Fig.6, Fig.7D and
- Page 1795 and 1796:
each first stator magnet 40, is loc
- Page 1797 and 1798:
Referring now to Fig.2, Fig.3, Fig.
- Page 1799 and 1800:
12 and three pairs 32 of U-shaped m
- Page 1801 and 1802:
about an armature axis of rotation
- Page 1803 and 1804:
Referring now to Fig.5, Fig.16 and
- Page 1805 and 1806:
otor 12. Further the number of abut
- Page 1807 and 1808:
11. The apparatus (10') of claim 7,
- Page 1809 and 1810:
causes the unpaired electrons to sp
- Page 1811 and 1812:
A - 49
- Page 1813 and 1814:
Fig.4, and the spinning electron pa
- Page 1815 and 1816:
the armature magnets for given magn
- Page 1817 and 1818:
23. The method of producing a unidi
- Page 1819 and 1820:
use of a rotating carousel which ca
- Page 1821 and 1822:
Fig.4 is a cross-sectional view of
- Page 1823 and 1824:
Fig.7 is a wave form showing flux l
- Page 1825 and 1826:
Fig.14 is a modification of the car
- Page 1827 and 1828:
surface of channel 28. This arrange
- Page 1829 and 1830:
the magnetic field. An examination
- Page 1831 and 1832:
induced in coil 17 is a function of
- Page 1833 and 1834:
The modified carousel structure 24'
- Page 1835 and 1836:
Notes: I found it a little difficul
- Page 1837 and 1838:
Fig.2 is a schematic layout of a hi
- Page 1839 and 1840:
Extending from switches 14 and 16 i
- Page 1841 and 1842:
Table 1 shows the data to be obtain
- Page 1843 and 1844:
Across a single fluorescent lamp, t
- Page 1845 and 1846:
HAROLD COLMAN & RONALD SEDDON-GILLE
- Page 1847 and 1848:
The ends of the quartz tube 13 are
- Page 1849 and 1850:
JONG-SOK AN: NO-LOAD GENERATOR Pate
- Page 1851 and 1852:
In short, the present invention is
- Page 1853 and 1854:
Fig.4 is an enlarged plan view of m
- Page 1855 and 1856:
BEST MODES FOR CARRYING OUT THE INV
- Page 1857 and 1858:
As shown in Fig.3, the coils are wo
- Page 1859 and 1860:
When electric power is to be genera
- Page 1861 and 1862:
As shown in Table 3 above, as the r
- Page 1863 and 1864:
SUMMARY OF THE INVENTION The Contin
- Page 1865 and 1866:
Fig.2 shows an internal wiring diag
- Page 1867 and 1868:
Fig.5 shows a wiring diagram for an
- Page 1869 and 1870:
Fig.8 shows the complete system of
- Page 1871 and 1872:
Fig.2 shows the three-phase arrange
- Page 1873 and 1874:
Once the generator is started, a sm
- Page 1875 and 1876:
MICHAEL OGNYANOV: SEMICONDUCTORS Pa
- Page 1877 and 1878:
Fig.3 is an electric circuit diagra
- Page 1879 and 1880:
The lead 39 is also connected to on
- Page 1881 and 1882:
EDWIN GRAY: ELECTRIC MOTOR US Paten
- Page 1883 and 1884:
Fig.1 is an explanatory schematic d
- Page 1885 and 1886:
Fig.5 is a sectional view taken at
- Page 1887 and 1888:
Fig.11 is a sectional view taken at
- Page 1889 and 1890:
Fig.14 is a sectional view, taken a
- Page 1891 and 1892:
Fig.19 is a developed view, taken a
- Page 1893 and 1894:
Referring to Fig.4, Fig.5 and Fig.9
- Page 1895 and 1896:
At a position 13.33 degrees to the
- Page 1897 and 1898:
start of a cycle are shown to corre
- Page 1899 and 1900:
Clutch 304 is associated with shaft
- Page 1901 and 1902:
in rotation by the successive disch
- Page 1903 and 1904:
Means for discharging said charged
- Page 1905 and 1906:
DESCRIPTION OF THE PREFERRED EMBODI
- Page 1907 and 1908:
inductance 36, inducing a strong el
- Page 1909 and 1910:
solid-state commutator, that closes
- Page 1911 and 1912:
2.7K cosmic background temperature
- Page 1913 and 1914:
disc. Also, the rotor may be mounte
- Page 1915 and 1916:
Fig.3 depicts the magnetisation act
- Page 1917 and 1918:
The fact that one can extract energ
- Page 1919 and 1920:
In the situation depicted in Fig.2
- Page 1921 and 1922:
the flux will be attracted through
- Page 1923 and 1924:
In the latter case it would still s
- Page 1925 and 1926:
otor, rotor magnetisation means inc
- Page 1927 and 1928:
unit of radium to the wire was elim
- Page 1929 and 1930:
The output coil is positioned so as
- Page 1931 and 1932:
Fig.2A is a perspective view schema
- Page 1933 and 1934:
Fig.6 is a perspective view of the
- Page 1935 and 1936:
Fig.9B is a schematic end-view of t
- Page 1937 and 1938:
The only physicist to recognise in
- Page 1939 and 1940:
like recoil of an electron when it
- Page 1941 and 1942:
In normal conductors, the inductive
- Page 1943 and 1944:
oscillating conditions. Thus, the r
- Page 1945 and 1946:
Turning now to Fig.2A, the sending
- Page 1947 and 1948:
The remaining surplus energy from t
- Page 1949 and 1950:
sending coil 20. This proportion of
- Page 1951 and 1952:
apparatus (at a sacrifice of some e
- Page 1953 and 1954:
The coil configuration of yet anoth
- Page 1955 and 1956:
the output voltage and current to b
- Page 1957 and 1958:
Planck, M., 1911, Verh. D. Deutsch.
- Page 1959 and 1960:
SUMMARY OF THE INVENTION It is thus
- Page 1961 and 1962:
Fig.4 is an alternate embodiment of
- Page 1963 and 1964:
an expanding and collapsing magneti
- Page 1965 and 1966:
that the inductive reactance is als
- Page 1967 and 1968:
Finally, the magnets are placed in
- Page 1969 and 1970:
Volts mA mW (a) Conventional method
- Page 1971 and 1972:
CM = conventional method; SI = subj
- Page 1973 and 1974:
5500 Turns 350 to 1200 RPM 350 to 1
- Page 1975 and 1976:
GEOFFREY SPENCE: ENERGY CONVERSION
- Page 1977 and 1978:
An external source is used to accel
- Page 1979 and 1980:
Fig.4 is a diagrammatic section thr
- Page 1981 and 1982:
Fig.8 is a section on line A--A of
- Page 1983 and 1984:
As shown more particularly in Fig.2
- Page 1985 and 1986:
A - 223
- Page 1987 and 1988:
As already mentioned, the converter
- Page 1989 and 1990:
22. A converter according to claim
- Page 1991 and 1992:
However, synchronous converters are
- Page 1993 and 1994:
Fig.4 is a typical duplicate of an
- Page 1995 and 1996:
cutting the magnetic lines of force
- Page 1997 and 1998:
elated to a common armature synchro
- Page 1999 and 2000:
For example, as shown in Fig.1A and
- Page 2001 and 2002:
Rotation position detecting means f
- Page 2003 and 2004:
Referring to Fig.2B, windings 7c an
- Page 2005 and 2006:
Fig.5A, Fig.5B and Fig.5C, show how
- Page 2007 and 2008:
Referring to a waveform of an outpu
- Page 2009 and 2010:
surfaces are N-poles. The arc-shape
- Page 2011 and 2012:
a first single-opposed-polarity rot
- Page 2013 and 2014:
14. The induction generator having
- Page 2015 and 2016:
Fig.1 is a partially sectioned elev
- Page 2017 and 2018:
Referring to Fig.1, a preferred emb
- Page 2019 and 2020:
A commutator 82 is also mounted on
- Page 2021 and 2022:
TERUO KAWAI: ELECTRIC MOTOR United
- Page 2023 and 2024:
Fig.2 is a sectional view along lin
- Page 2025 and 2026:
Fig.4A through Fig.4H illustrate op
- Page 2027 and 2028:
A - 265
- Page 2029 and 2030:
Fig.5A is an illustrative view show
- Page 2031 and 2032:
FIGS. 6 through 9 are cross-section
- Page 2033 and 2034:
FIGS. 10A through 10C are cross-sec
- Page 2035 and 2036:
A - 273
- Page 2037 and 2038:
through 16l is arranged so as to be
- Page 2039 and 2040:
According to this modified embodime
- Page 2041 and 2042:
The sequential excitation of the el
- Page 2043 and 2044:
All of the prior art systems are de
- Page 2045 and 2046:
Fig.4 is a schematic view in genera
- Page 2047 and 2048:
-First Embodiment (Fig.1) One possi
- Page 2049 and 2050:
A. Related Principles 1. Numerous s
- Page 2051 and 2052:
material. This same effect shows up
- Page 2053 and 2054:
In the second prototype embodiment
- Page 2055 and 2056:
The 14-gauge and 15-gauge insulated
- Page 2057 and 2058:
Because many varying and different
- Page 2059 and 2060:
particles making up or coming from
- Page 2061 and 2062:
ceramics, and which take advantage
- Page 2063 and 2064:
Fig.4 is a graphical illustration o
- Page 2065 and 2066:
Fig.8 is a diagram illustrating the
- Page 2067 and 2068:
Fig.11 is a diagram illustrating th
- Page 2069 and 2070:
Fig.15 is a diagram illustrating ph
- Page 2071 and 2072:
Fig.19 is a cross-sectional, elevat
- Page 2073 and 2074:
Fig.23 is an illustration depicting
- Page 2075 and 2076:
Fig.29 is a schematic illustration
- Page 2077 and 2078:
Fig.33 is a schematic illustration
- Page 2079 and 2080:
For a given composition the photo-e
- Page 2081 and 2082:
Polishing the surfaces of these mat
- Page 2083 and 2084:
n o and s, from this and the three
- Page 2085 and 2086:
A - 323
- Page 2087 and 2088:
A - 325
- Page 2089 and 2090:
The implication is therefore that p
- Page 2091 and 2092:
Which compares with an observed ban
- Page 2093 and 2094:
Initially, a polarisation voltage i
- Page 2095 and 2096:
with reflected light. The surface o
- Page 2097 and 2098:
specification would be produced by
- Page 2099 and 2100:
24. A display apparatus as defined
- Page 2101 and 2102:
SUMMARY OF THE INVENTION These and
- Page 2103 and 2104:
Fig.4 is a side view of two magneti
- Page 2105 and 2106:
A - 343
- Page 2107 and 2108:
Figs.11, 11A-11F are side views of
- Page 2109 and 2110:
Figs.12, 12A-12E are side views of
- Page 2111 and 2112:
A - 349
- Page 2113 and 2114:
Figs.17A-17D depict another embodim
- Page 2115 and 2116:
Fig.19 is an exploded perspective v
- Page 2117 and 2118:
Figs.21A-21E are top views of the p
- Page 2119 and 2120:
Fig.24 is a perspective view of the
- Page 2121 and 2122:
Fig.31 is a perspective view of the
- Page 2123 and 2124:
Fig.36 is a perspective view of the
- Page 2125 and 2126:
Figs.40-44 are alternative variatio
- Page 2127 and 2128:
A - 365
- Page 2129 and 2130:
Fig.49 is a top view of another emb
- Page 2131 and 2132:
In Fig.2 a device 40 having the sam
- Page 2133 and 2134:
pole pieces 94, 96 due to the resul
- Page 2135 and 2136:
Fig.10D depicts another four-path c
- Page 2137 and 2138:
238 from coils 230 and 232 also tra
- Page 2139 and 2140:
Coils 286, 288 may be energised in
- Page 2141 and 2142:
This is demonstrated with reference
- Page 2143 and 2144:
This is demonstrated with reference
- Page 2145 and 2146:
Another embodiment of a device 400
- Page 2147 and 2148:
could also be achieved. It is also
- Page 2149 and 2150:
Referring to Fig.21C, just after ro
- Page 2151 and 2152:
In another embodiment, a rotary mot
- Page 2153 and 2154:
otor member 622 having notches 624
- Page 2155 and 2156:
A third embodiment of a rotary moti
- Page 2157 and 2158:
which detects the initial direction
- Page 2159 and 2160:
after permanent magnet rotor region
- Page 2161 and 2162:
Power Conversion Referring to Figs.
- Page 2163 and 2164:
With continuous flux paths the stat
- Page 2165 and 2166:
Fig.47 and Fig.48 show another embo
- Page 2167 and 2168:
one direction and the second path p
- Page 2169 and 2170:
(c) placing a first control coil al
- Page 2171 and 2172:
28. The device for producing rotor
- Page 2173 and 2174:
STEPHEN PATRICK et Al: THE MEG Unit
- Page 2175 and 2176:
driving the reversing means of one
- Page 2177 and 2178:
Figure 3 is a graphical view of dri
- Page 2179 and 2180:
Figure 8 is a graphical view of a c
- Page 2181 and 2182:
DETAILED DESCRIPTION OF THE INVENTI
- Page 2183 and 2184:
period of time longer than that nec
- Page 2185 and 2186:
Each of the permanent magnets 154 i
- Page 2187 and 2188:
6. The electromagnetic generator of
- Page 2189 and 2190:
DAN DAVIDSON: ACOUSTIC-MAGNETIC POW
- Page 2191 and 2192:
BRIEF DESCRIPTION OF THE DRAWINGS F
- Page 2193 and 2194:
DETAILED DESCRIPTION OF THE INVENTI
- Page 2195 and 2196:
1. An acoustic magnetic power gener
- Page 2197 and 2198:
For the power-out phase, energy is
- Page 2199 and 2200:
design of this new motor directs th
- Page 2201 and 2202:
Fig.3 is a block diagram demonstrat
- Page 2203 and 2204:
Fig.2 is a mechanical perspective t
- Page 2205 and 2206:
through winding 13a) exceeds the fl
- Page 2207 and 2208:
JOHN BEDINI: MOTOR/GENERATOR US Pat
- Page 2209 and 2210:
etained by the rotor and flywheel c
- Page 2211 and 2212:
By definition, this means that the
- Page 2213 and 2214:
SUMMARY OF THE INVENTION The device
- Page 2215 and 2216:
Fig.3 is a box diagram showing the
- Page 2217 and 2218:
Collector lead 33 and ground lead 3
- Page 2219 and 2220:
store a timed initial pulse charge.
- Page 2221 and 2222:
Fig.2 is a schematic drawing of a c
- Page 2223 and 2224:
Fig.5 is a block diagram of the sol
- Page 2225 and 2226:
direction into either channel one t
- Page 2227 and 2228:
Fig.3 is a schematic drawing of an
- Page 2229 and 2230:
8. The pulse-charger of claim 1 whe
- Page 2231 and 2232:
Notes: The following information is
- Page 2233 and 2234:
claim to have the highest power-per
- Page 2235 and 2236:
electrode pattern is applied with n
- Page 2237 and 2238:
Fig.3 is side view of a single-laye
- Page 2239 and 2240:
Composition-modified barium titanat
- Page 2241 and 2242:
FW d g/mol g/cm 3 Barium titanate B
- Page 2243 and 2244:
* ε o = permittivity of free space
- Page 2245 and 2246:
n) assembling the first arrays into
- Page 2247 and 2248:
HERMANN PLAUSON US Patent 1,540,998
- Page 2249 and 2250:
Fig.5 is a diagram of an arrangemen
- Page 2251 and 2252:
Fig.13 shows a form of inductive co
- Page 2253 and 2254:
Fig.21 shows diagramatically, an ar
- Page 2255 and 2256:
A - 493
- Page 2257 and 2258:
Fig.28 shows an auto-transformer me
- Page 2259 and 2260:
Fig.31 is a modified arrangement. F
- Page 2261 and 2262:
Fig.34 shows an arc light collector
- Page 2263 and 2264:
Fig.37 shows a form with a gas flam
- Page 2265 and 2266:
In addition to the use of spark gap
- Page 2267 and 2268:
In Fig.7 the oscillation circuit is
- Page 2269 and 2270:
As this prevents the whole of the o
- Page 2271 and 2272:
In order to collect large quantitie
- Page 2273 and 2274:
desired height, leads to a metal ro
- Page 2275 and 2276:
In Fig.26, 1,2,3 and 4 are metallic
- Page 2277 and 2278:
place, the necessary means are in p
- Page 2279 and 2280:
As transformer of the atmospheric e
- Page 2281 and 2282:
The metallic balloon shell which ha
- Page 2283 and 2284:
The action is exactly the same as t
- Page 2285 and 2286:
The novelty in this invention is: (
- Page 2287 and 2288:
DESCRIPTION OF THE DRAWINGS Fig.1 i
- Page 2289 and 2290:
Fig.6 is an enlarged detail fragmen
- Page 2291 and 2292:
assume any of several well known em
- Page 2293 and 2294:
While the magnets mentioned through
- Page 2295 and 2296:
the optimal distance between dipole
- Page 2297 and 2298:
coupled secondary two electric flux
- Page 2299 and 2300:
In none of the other motor solution
- Page 2301 and 2302:
Fig.2 is a schematic view of a Tesl
- Page 2303 and 2304:
Fig.12 shows apparatus for investig
- Page 2305 and 2306:
Fig.18 is a diagrammatic cross-sect
- Page 2307 and 2308:
positively, no positive ionise can
- Page 2309 and 2310:
We propose that likewise, if a very
- Page 2311 and 2312:
In our loss of weight experiments d
- Page 2313 and 2314:
energy injection and its dependency
- Page 2315 and 2316:
These results suggest that plasmas
- Page 2317 and 2318:
constant current flows through a ro
- Page 2319 and 2320:
The results indicate that the highe
- Page 2321 and 2322:
motor is set into motion, and is re
- Page 2323 and 2324:
PAULO and ALEXANDRA CORREA US Paten
- Page 2325 and 2326:
Fig.1 shows variation of applied DC
- Page 2327 and 2328:
Fig.6 shows volt amplitude variatio
- Page 2329 and 2330:
Fig.10A, Fig.10B and Fig.10C are fr
- Page 2331 and 2332:
Fig.13 shows open circuit voltage r
- Page 2333 and 2334:
Fig.16 shows resistive discharge sl
- Page 2335 and 2336:
Fig.20 shows an example of operatio
- Page 2337 and 2338:
the plate. There are other factors
- Page 2339 and 2340:
From the start our objective was to
- Page 2341 and 2342:
The circuit of Fig.10 can be integr
- Page 2343 and 2344:
20% to 70%), anywhere within the ra
- Page 2345 and 2346:
eflects the charge accumulation occ
- Page 2347 and 2348:
If the break-even efficiency is les
- Page 2349 and 2350:
With the data obtained by the metal
- Page 2351 and 2352:
plasma generation and collapse intr
- Page 2353 and 2354:
cathode work function is not due to
- Page 2355 and 2356:
Early interpretations attributed th
- Page 2357 and 2358:
etween the two states of a system.
- Page 2359 and 2360:
A - 597
- Page 2361 and 2362:
A - 599
- Page 2363 and 2364:
CLAIMS 1. Apparatus comprising a di
- Page 2365 and 2366:
FRANKLIN MEAD AND JACK NACHAMKIN Pa
- Page 2367 and 2368:
which partially encloses the receiv
- Page 2369 and 2370:
Fig.3 is a perspective view of the
- Page 2371 and 2372:
Fig.6 is a diagram of a receiving s
- Page 2373 and 2374:
Referring to the drawings, a first
- Page 2375 and 2376:
A - 613
- Page 2377 and 2378:
A - 615
- Page 2379 and 2380:
A - 617
- Page 2381 and 2382:
A - 619
- Page 2383 and 2384:
Fig.2 Shows a perspective of a "wat
- Page 2385 and 2386:
The overall apparatus thus includes
- Page 2387 and 2388:
and the water molecule becomes elon
- Page 2389 and 2390:
STANLEY MEYER US Patent 4,389,981 2
- Page 2391 and 2392:
Fig.2 is a block schematic illustra
- Page 2393 and 2394:
Fig.9 is a comparison of the burnin
- Page 2395 and 2396:
The mixture of air with non-combust
- Page 2397 and 2398:
Fig.7 illustrates the mechanical ar
- Page 2399 and 2400:
STANLEY MEYER US Patent 4,421,474 D
- Page 2401 and 2402:
BRIEF DESCRIPTION OF THE DRAWINGS F
- Page 2403 and 2404:
plate adjustment 15 for controlling
- Page 2405 and 2406:
Fig.2 illustrates a circuit which i
- Page 2407 and 2408:
Fig.5A shows a cross-section of a c
- Page 2409 and 2410:
Figs.6A, 6B, 6C and 6D are illustra
- Page 2411 and 2412:
Fig.7 is an electrical schematic of
- Page 2413 and 2414:
A fuel gas is produced by a hydroge
- Page 2415 and 2416:
The primary coil of the torroid is
- Page 2417 and 2418:
material of construction for the el
- Page 2419 and 2420:
applied is repetitive without polar
- Page 2421 and 2422:
STANLEY MEYER Canadian Patent 2,067
- Page 2423 and 2424:
Fig.2B is a frontal view from the o
- Page 2425 and 2426:
Fig.4 shows a disk array of injecto
- Page 2427 and 2428:
Table 1 Injector Mixture + Process
- Page 2429 and 2430:
distorted in shape by being subject
- Page 2431 and 2432:
Example 5 Fuel distribution and man
- Page 2433 and 2434:
addition, the gated pulse frequency
- Page 2435 and 2436:
Fig.4 is a voltage amplitude contro
- Page 2437 and 2438:
Fig.9 is the pulse indicator circui
- Page 2439 and 2440:
The circuits are interconnected as
- Page 2441 and 2442:
CLAIMS 1. A control circuit for a r
- Page 2443 and 2444:
DETAILED DESCRIPTION OF THE DRAWING
- Page 2445 and 2446:
Fig.4 shows the electrical circuits
- Page 2447 and 2448:
eference point 0V. It is this bias
- Page 2449 and 2450:
The production cycle is repeated un
- Page 2451 and 2452:
Dr HENRY PUHARICH Dr Andrija Puhari
- Page 2453 and 2454:
The Thermodynamic Device (“TD”)
- Page 2455 and 2456:
Component 3: The weak electrolyte w
- Page 2457 and 2458:
meter. Corollary to this finding, I
- Page 2459 and 2460:
and P = I x E =38 mA x 2.6 volts =
- Page 2461 and 2462:
Then, 5,739 C /cc /sec = 5.739 amp/
- Page 2463 and 2464:
Fig.2 is a schematic illustration o
- Page 2465 and 2466:
Fig.4C is an illustration of the ge
- Page 2467 and 2468:
Fig.8 is an illustration of tetrahe
- Page 2469 and 2470:
Fig.11 is a wave form found to be t
- Page 2471 and 2472:
DETAILED DESCRIPTION OF INVENTION:
- Page 2473 and 2474:
not so great and the bond angle is
- Page 2475 and 2476:
As the outer electrode becomes more
- Page 2477 and 2478:
The energy which must be supplied f
- Page 2479 and 2480:
The electrical energy required to l
- Page 2481 and 2482:
SHIGETA HASEBE US Patent 4,105,528
- Page 2483 and 2484:
Fig.2 is a perspective view of elec
- Page 2485 and 2486:
produce a transverse field, and thr
- Page 2487 and 2488:
STEPHEN CHAMBERS (Xogen Power Inc.)
- Page 2489 and 2490:
BRIEF DESCRIPTION OF THE DRAWINGS F
- Page 2491 and 2492:
Fig.3 is a side view of a cell for
- Page 2493 and 2494:
Fig.5 is an electronic circuit diag
- Page 2495 and 2496:
Fig.8 is a side view of a cell for
- Page 2497 and 2498:
The cell includes a closed containe
- Page 2499 and 2500:
the cell of the present invention i
- Page 2501 and 2502:
Vcc. Resistor R1 ensures that TR4 i
- Page 2503 and 2504:
Figure 1 is a view in vertical sect
- Page 2505 and 2506:
Figure 3 is a diagrammatic view of
- Page 2507 and 2508:
Water under pressure is forced into
- Page 2509 and 2510:
In order to provide for alternate e
- Page 2511 and 2512:
Fig.1 is a diagrammatic elevational
- Page 2513 and 2514:
The cell as shown in Fig.1 comprise
- Page 2515 and 2516:
1. A process for producing, Through
- Page 2517 and 2518:
The main process in these invention
- Page 2519 and 2520:
Fig.1 and Fig.2 are illustrations o
- Page 2521 and 2522:
Fig.4 is a schematic diagram of a p
- Page 2523 and 2524:
Next provided is an axially shifted
- Page 2525 and 2526:
evident function of minimising the
- Page 2527 and 2528:
partial vacuum. This reduction in p
- Page 2529 and 2530:
as an essential feature of the inve
- Page 2531 and 2532:
In the case of water, hydrogen and
- Page 2533 and 2534:
Fig.3 is a schematic sectional fron
- Page 2535 and 2536:
Fig.7 is a schematic graph of curre
- Page 2537 and 2538:
Continuous light spots may also be
- Page 2539 and 2540:
thousand times atmospheric pressure
- Page 2541 and 2542:
Fig.2 illustrates a variation on th
- Page 2543 and 2544:
oadly, a liquid container in the fo
- Page 2545 and 2546:
The glow discharge causes the gener
- Page 2547 and 2548:
A - 785
- Page 2549 and 2550:
Tube in tube reactor (Fig.17) has a
- Page 2551 and 2552:
The under-liquid plasma discharge,
- Page 2553 and 2554:
ecoming vigorous when the voltage i
- Page 2555 and 2556:
TABLE 2 - The micro-organism count
- Page 2557 and 2558:
The gas trap or chamber should be o
- Page 2559 and 2560:
space either in the metal electrode
- Page 2561 and 2562:
1.3.2 Equipment Function: DC power
- Page 2563 and 2564:
construction on one side or both si
- Page 2565 and 2566:
The problem of pollution is a major
- Page 2567 and 2568:
Some chemical contaminants can only
- Page 2569 and 2570:
A - 807
- Page 2571 and 2572:
A - 809
- Page 2573 and 2574:
A - 811
- Page 2575 and 2576:
A - 813
- Page 2577 and 2578:
A - 815
- Page 2579 and 2580:
A - 817
- Page 2581 and 2582:
A - 819
- Page 2583 and 2584:
A - 821
- Page 2585 and 2586:
Juan Aguero’s Water-Fuel Engine P
- Page 2587 and 2588:
and is mixed with the intake air. P
- Page 2589 and 2590:
combustion chambers. The hydrogen i
- Page 2591 and 2592:
21. The system of claim 20, charact
- Page 2593 and 2594:
storage. The present invention enab
- Page 2595 and 2596:
Fig.4 is an elevation view of the h
- Page 2597 and 2598:
Fig.10 is a cross-section on the li
- Page 2599 and 2600:
Fig.16 is a cross-section on the li
- Page 2601 and 2602:
Fig.23 is an enlargement of part of
- Page 2603 and 2604:
Fig.33 is a perspective view of a v
- Page 2605 and 2606:
A - 843
- Page 2607 and 2608:
through a resistor R4 to provide tr
- Page 2609 and 2610:
The installation of the above circu
- Page 2611 and 2612:
cathode in the upper region of the
- Page 2613 and 2614:
transformer and, assuming an input
- Page 2615 and 2616:
valve apparatus to control engine s
- Page 2617 and 2618:
. a first hollow cylindrical electr
- Page 2619 and 2620:
The Water Fracture Cell of Christop
- Page 2621 and 2622:
Fig.1 is a circuit diagram of fract
- Page 2623 and 2624:
If a large electric field is applie
- Page 2625 and 2626:
The pulses R1 and S1 are of the sam
- Page 2627 and 2628:
water ions to generate hydrogen and
- Page 2629 and 2630:
A - 867
- Page 2631 and 2632:
Fig.5B shows a stylised representat
- Page 2633 and 2634:
Fig.6 shows a gas collection system
- Page 2635 and 2636:
Fig.8A and Fig.8B are views of a se
- Page 2637 and 2638:
A - 875
- Page 2639 and 2640:
Figs.16-30 are graphs supporting th
- Page 2641 and 2642:
A - 879
- Page 2643 and 2644:
A - 881
- Page 2645 and 2646:
A - 883
- Page 2647 and 2648:
A - 885
- Page 2649 and 2650:
A - 887
- Page 2651 and 2652:
If it is the case that the hydrogen
- Page 2653 and 2654:
plate shown in Fig.1A and Fig.1B an
- Page 2655 and 2656:
is in equilibrium where the 10 watt
- Page 2657 and 2658:
The previously mentioned prior art
- Page 2659 and 2660:
The stores of high pressure gases c
- Page 2661 and 2662:
unit to retain operational gas pres
- Page 2663 and 2664:
Henry Paine’s HHO Fuel Conversion
- Page 2665 and 2666:
Witnesses: Bennet Osborne, Jr., W.
- Page 2667 and 2668:
However, the electromagnetic propul
- Page 2669 and 2670:
coils. Thus, Podkletnov's system is
- Page 2671 and 2672:
Fig.2A and Fig.2B are diagrams, pre
- Page 2673 and 2674:
Fig.4A and Fig.4B are diagrams, pre
- Page 2675 and 2676:
#1 hollow superconductive shield #2
- Page 2677 and 2678:
Fig.2B shows the counter-clockwise
- Page 2679 and 2680:
In this example, the difference bet
- Page 2681 and 2682:
The First High MPG Carburettor of C
- Page 2683 and 2684:
Fig.3 is a horizontal sectional vie
- Page 2685 and 2686:
Fig.9 and Fig.10 are detail section
- Page 2687 and 2688:
having a valve 52 in it. Chamber 50
- Page 2689 and 2690:
The Second High MPG Carburettor of
- Page 2691 and 2692:
Fig.4 is a detail sectional view of
- Page 2693 and 2694:
A low-speed or idling jet 25 has it
- Page 2695 and 2696:
DESCRIPTION OF THE DRAWINGS Fig.1 i
- Page 2697 and 2698:
Fig.5 is a detail sectional view on
- Page 2699 and 2700:
Vapour formed by air bubbling throu
- Page 2701 and 2702:
From the foregoing description it w
- Page 2703 and 2704:
Fig.2 is an enlarged view of the de
- Page 2705 and 2706:
Fig.6 is a section taken along line
- Page 2707 and 2708:
The High MPG Carburettor of Robert
- Page 2709 and 2710:
Fig.4 is a transverse sectional vie
- Page 2711 and 2712:
The High MPG Carburettor of Harold
- Page 2713 and 2714:
182,420 now abandoned. The present
- Page 2715 and 2716:
DESCRIPTION OF THE INVENTION The ca
- Page 2717 and 2718:
The High MPG Carburettor of Thomas
- Page 2719 and 2720:
In accordance with other aspects of
- Page 2721 and 2722:
Fig.3 is a sectional view of the va
- Page 2723 and 2724:
Fig.7 is a partial side, partial se
- Page 2725 and 2726:
The cooling system of the vehicle c
- Page 2727 and 2728:
Upon initial starting of the engine
- Page 2729 and 2730:
(f) A filter positioned in the vapo
- Page 2731 and 2732:
with the magnitude of the current a
- Page 2733 and 2734:
Fig.1B is a perspective view of the
- Page 2735 and 2736:
Fig.3 is a top view of the motor of
- Page 2737 and 2738:
Fig.7 is an isometric view showing
- Page 2739 and 2740:
Fig.10 is a top view showing the ro
- Page 2741 and 2742:
Fig.13 is a top view of a pair of r
- Page 2743 and 2744:
Extending in opposite diametric dir
- Page 2745 and 2746:
Fig.5 shows the state of the switch
- Page 2747 and 2748:
otor magnets 42 - 49 when in the ho
- Page 2749 and 2750:
Fig.9 and Fig.10 show a second arra
- Page 2751 and 2752:
constructed otherwise than as speci
- Page 2753 and 2754:
12. The motor of claim 11 wherein t
- Page 2755 and 2756:
otation between them. Various metho
- Page 2757 and 2758:
Fig.4 is a view similar to Fig.3 bu
- Page 2759 and 2760:
Fig.10 is a view similar to Fig.3 f
- Page 2761 and 2762:
Fig.13 is a schematic circuit diagr
- Page 2763 and 2764:
Fig.16 is a simplified embodiment o
- Page 2765 and 2766:
Fig.22 to Fig.25 are similar to Fig
- Page 2767 and 2768:
Referring to Fig.2, the permanent m
- Page 2769 and 2770:
Fig.7 shows a modified embodiment w
- Page 2771 and 2772:
them, will depend upon the order in
- Page 2773 and 2774:
Fig.14, shows another embodiment 14
- Page 2775 and 2776:
Fig.18 shows the air coil 210 posit
- Page 2777 and 2778:
Figs. 22-25 show four different pos
- Page 2779 and 2780:
movement with the first permanent m
- Page 2781 and 2782:
a shaft and means journaling the sh
- Page 2783 and 2784:
The Power Plant of Claude Mead and
- Page 2785 and 2786:
Fig.2 is a front elevation of the w
- Page 2787 and 2788:
impactors and drills. The turbine d
- Page 2789 and 2790:
(a) fourth rotating means responsiv
- Page 2791 and 2792:
ing-shaped magnetic core having a m
- Page 2793 and 2794:
Fig.3 is an oscilloscope waveform t
- Page 2795 and 2796:
DETAILED DESCRIPTION OF THE PREFERR
- Page 2797 and 2798:
although it is by no means obvious
- Page 2799 and 2800:
second diode connected at its posit
- Page 2801 and 2802:
iron, the useful ability to aim, fo
- Page 2803 and 2804:
Fig.4 is a circuit diagram, illustr
- Page 2805 and 2806:
and Fig.3. In practice, this coil m
- Page 2807 and 2808:
y a simultaneous magnetic accelerat
- Page 2809 and 2810:
Mr. P.G. Mallory started out in 191
- Page 2811 and 2812:
All models have a 30 Watt power rat
- Page 2813 and 2814:
In the auto racing circles it has a
- Page 2815 and 2816:
PULSE GENERATOR 'PICK UP' SIMPLIFIE
- Page 2817 and 2818:
Schematic Wiring Diagrams for two P
- Page 2819 and 2820:
motor. What is not generally known,
- Page 2821 and 2822:
Mark McKay's investigation of Edwin
- Page 2823 and 2824:
Investor Photo #012D Popping a coil
- Page 2825 and 2826:
capacitors connected in series, wit
- Page 2827 and 2828:
Mark McKay's investigation of Edwin
- Page 2829 and 2830:
Observing the lack of wear, the new
- Page 2831 and 2832:
TOP DEAD CENTER 0° REFERENCE Accor
- Page 2833 and 2834:
Mark McKay's investigation of Edwin
- Page 2835 and 2836:
The recovery and simple analysis of
- Page 2837 and 2838:
MAGNETIC POSITION PROBE SMALL RED F
- Page 2839 and 2840:
Subject: CSET design Date: Sun Feb
- Page 2841 and 2842:
Date: Fri Feb 28, 2003 8:25 pm (Tim
- Page 2843 and 2844:
(Tad Johnson) I'm being as careful
- Page 2845 and 2846:
SANGAMO ENERGY DISCHARGE CAPACITOR
- Page 2847 and 2848:
(Alan Francoeur) But I also measure
- Page 2849 and 2850:
Subject: Progress Date: Sun Mar 30,
- Page 2851 and 2852:
● COMMENTARY: This really limits
- Page 2853 and 2854:
Mark Gray claims that the heart and
- Page 2855 and 2856:
Mark Gray claims that some potentia
- Page 2857 and 2858:
General Signal Generator Pulse Gene
- Page 2859 and 2860:
Mark McKay's investigation of Edwin
- Page 2861 and 2862:
Some time during 1987 - 1988, Gray
- Page 2863 and 2864:
The two-channel trace from the osci
- Page 2865 and 2866:
What “maximum squareness” means
- Page 2867 and 2868:
Z o = 112 Ohms T d of 293 nS. 50 KV
- Page 2869 and 2870:
Mike Brady’s “Perendev” Magne
- Page 2871 and 2872:
Fig.3 is a perspective view showing
- Page 2873 and 2874:
Fig.7 is a perspective view showing
- Page 2875 and 2876:
In the rotor assembly 30 of Fig.2,
- Page 2877 and 2878:
Fig.7 shows a typical magnetic sour
- Page 2879 and 2880:
The Magnet Motor of Donald A. Kelly
- Page 2881 and 2882:
This magnetic disc drive represents
- Page 2883 and 2884:
Fig.1 is a top, external view of th
- Page 2885 and 2886:
Multiple, identical permanent magne
- Page 2887 and 2888:
Bob Neal’s Compressed Air Engine
- Page 2889 and 2890:
Fig.3 is a vertical cross-sectional
- Page 2891 and 2892:
The inner ends of the cylinders 11
- Page 2893 and 2894:
In the equaliser 75, are the spaced
- Page 2895 and 2896:
which changes the valve timing of a
- Page 2897 and 2898:
Fig.3 is a cross-sectional view tak
- Page 2899 and 2900:
A - 1137
- Page 2901 and 2902:
DETAILED DESCRIPTION OF THE PREFERR
- Page 2903 and 2904:
With reference to Fig.3, a pluralit
- Page 2905 and 2906:
A contact 75, biased towards the an
- Page 2907 and 2908:
plate having an opening in the cent
- Page 2909 and 2910:
advantageous to rearrange the exhau
- Page 2911 and 2912:
Fig.2 is a fragmentary perspective
- Page 2913 and 2914:
The turbine 16 embodies a stator co
- Page 2915 and 2916:
In an operative embodiment of the i
- Page 2917 and 2918:
Briefly, in one aspect the engine o
- Page 2919 and 2920:
Fig.5 is a cross-sectional view of
- Page 2921 and 2922:
Fig.12 is a cross-sectional view si
- Page 2923 and 2924:
Fig.14 is a schematic diagram of an
- Page 2925 and 2926:
A - 1163
- Page 2927 and 2928:
A - 1165
- Page 2929 and 2930:
Figs.20A-20F are schematic diagrams
- Page 2931 and 2932:
Note: Corresponding reference chara
- Page 2933 and 2934:
Integral with the piston bodies are
- Page 2935 and 2936:
The piston has a generally semi-tor
- Page 2937 and 2938:
Referring back to Fig.13A, for engi
- Page 2939 and 2940:
As piston 39A reaches BDC, distribu
- Page 2941 and 2942:
mixture and do not combine because
- Page 2943 and 2944:
These wires are about twelve gauge,
- Page 2945 and 2946:
cold-cathode tube 391, and an x-ray
- Page 2947 and 2948:
Fig.17D), polariser 289, branch B17
- Page 2949 and 2950:
Robert Britt’s Inert Gas Engine U
- Page 2951 and 2952:
Fig.3 is an elevational view of the
- Page 2953 and 2954:
Fig.7 is an electrical schematic of
- Page 2955 and 2956:
Referring now to Fig.3 of the drawi
- Page 2957 and 2958:
and drives Q1 into conduction. The
- Page 2959 and 2960:
Floyd Sweet Recently, some addition
- Page 2961 and 2962:
the venture capital funding if the
- Page 2963 and 2964:
Violet also said that about 5:00 pm
- Page 2965 and 2966:
Energy cannot enter a space of zero
- Page 2967 and 2968:
electromagnetic and gravitational f
- Page 2969 and 2970:
or in another form: So, the e.m.f.
- Page 2971 and 2972:
Example 2: Suppose the conductor wi
- Page 2973 and 2974:
Meguer Kalfaian’s Energy Generato
- Page 2975 and 2976:
Fig.2 illustrates a controlled top
- Page 2977 and 2978:
Fig.9 is a modification of Fig.6; a
- Page 2979 and 2980:
the outer periphery of the magnet,
- Page 2981 and 2982:
wobbling top is sufficient, as proo
- Page 2983 and 2984:
Theodore Annis & Patrick Eberly US
- Page 2985 and 2986:
BRIEF DESCRIPTION OF THE DRAWINGS F
- Page 2987 and 2988:
Fig.6 is a schematic diagram of a s
- Page 2989 and 2990:
Fig.1 is a schematic diagram of a m
- Page 2991 and 2992:
Fig.5 is a detail drawing of an alt
- Page 2993 and 2994:
In the preferred implementation of
- Page 2995 and 2996:
The Energy Conversion Device of Wil
- Page 2997 and 2998:
This sloping floor causes the drive
- Page 2999 and 3000:
FIG.4 is a cross-sectional view of
- Page 3001 and 3002:
FIG.9 is a horizontal cross-section
- Page 3003 and 3004:
otational downstream annular chambe
- Page 3005 and 3006:
In Fig.5 is shown a perspective vie
- Page 3007 and 3008:
small hydro-electric version of the
- Page 3009 and 3010:
Fig.10 is a perspective view of a s
- Page 3011 and 3012:
longitudinally mounted in the upstr
- Page 3013 and 3014:
shaft in the central aperture, said
- Page 3015 and 3016:
The ‘Hotsabi’ Booster Here are
- Page 3017 and 3018:
Cut and fit shimstock into ABS tubi
- Page 3019 and 3020:
The upper component is a Threaded A
- Page 3021 and 3022:
Next, prepare the stainless steel m
- Page 3023 and 3024:
All of the 3/8 inch plastic fitting
- Page 3025 and 3026:
If you choose to use a contact-brea
- Page 3027 and 3028:
This booster uses cheap, standard e
- Page 3029 and 3030:
In order to ensure that the stainle
- Page 3031 and 3032:
The picture above shows clearly the
- Page 3033 and 3034:
The PVC housing for the booster has
- Page 3035 and 3036:
But, it can be built using differen
- Page 3037 and 3038:
Try to make the hose as short as po
- Page 3039 and 3040:
Background Information Many people
- Page 3041 and 3042:
This diagram shows the way that the
- Page 3043 and 3044:
Dealing with the Vehicle Computer W
- Page 3045 and 3046:
This unit generates a small voltage
- Page 3047 and 3048:
think that the Air/Fuel Ratio is sa
- Page 3049 and 3050:
something similar to provide non-li
- Page 3051 and 3052:
The 1N4007 diode has a ring marked
- Page 3053 and 3054:
are needed to feed the incoming sen
- Page 3055 and 3056:
“voltage divider” and it is the
- Page 3057 and 3058:
This gives us a voltage in the corr
- Page 3059 and 3060:
The tools which you will need, are:
- Page 3061 and 3062:
To construct this circuit, cut a pi
- Page 3063 and 3064:
And for a UK supplier: Component Qt
- Page 3065 and 3066:
The High Efficiency Electrolyser de
- Page 3067 and 3068:
If the voltage is increased above 1
- Page 3069 and 3070:
about 1.5 volts. This means that a
- Page 3071 and 3072:
The one-way valve shown between the
- Page 3073 and 3074:
The base and two sides of the cell
- Page 3075 and 3076:
This housing looks very simple and
- Page 3077 and 3078:
Any particles created by the sandin
- Page 3079 and 3080:
3. If current starts higher then dr
- Page 3081 and 3082:
different suppliers, can have sligh
- Page 3083 and 3084:
Terminal Block TB1: is the DC Power
- Page 3085 and 3086:
quickly destroyed. The Texas Instru
- Page 3087 and 3088:
As you can see here, Bob uses short
- Page 3089 and 3090:
touching each other in the centre o
- Page 3091 and 3092:
With straight DC-electrolysis, the
- Page 3093 and 3094:
Supplying the Water The potassium h
- Page 3095 and 3096:
Components: R1 100 ohms C1 1000 mic
- Page 3097 and 3098:
pressure of just 15 psi. To deal wi
- Page 3099 and 3100:
Also, the pressure at which it oper
- Page 3101 and 3102:
nothing is done about that, a decre
- Page 3103 and 3104:
The physical connection to the engi
- Page 3105 and 3106:
One supplier of flexible tubing sui
- Page 3107 and 3108:
Bob Boyce’s Experiences: Bob had
- Page 3109 and 3110:
Suggested Design Features for High-
- Page 3111 and 3112:
Bob uses a 6-inch x 48-inch belt sa
- Page 3113 and 3114:
there is a major problem. Make sure
- Page 3115 and 3116:
This plate array can be a self-cont
- Page 3117 and 3118:
shatter discs seem attractive optio
- Page 3119 and 3120:
shown with a baffle, but with stati
- Page 3121 and 3122:
The High-Power Devices of Don Smith
- Page 3123 and 3124:
Fig.2 has two parts A and B. In Fig
- Page 3125 and 3126:
The device shown below is physicall
- Page 3127 and 3128:
The entire System already exists an
- Page 3129 and 3130:
Don Smith's Suggestions: Get a copy
- Page 3131 and 3132:
A - 1369
- Page 3133 and 3134:
*************************** PJK: I
- Page 3135 and 3136:
However, if we want to extract ener
- Page 3137 and 3138:
If the swing is pushed before it re
- Page 3139 and 3140:
Without his description of the devi
- Page 3141 and 3142:
Anyway, coming back to Don's device
- Page 3143 and 3144:
The "L2" coil has two separate sect
- Page 3145 and 3146:
In passing, it might be remarked th
- Page 3147 and 3148:
Don draws attention to the fact tha
- Page 3149 and 3150:
The objective here is to determine
- Page 3151 and 3152:
I have recently been passed a copy
- Page 3153 and 3154:
contains substantially more power t
- Page 3155 and 3156:
number of primary winding turns. Wi
- Page 3157 and 3158:
And to make matters ‘worse’ the
- Page 3159 and 3160:
Here, the additional high-voltage d
- Page 3161 and 3162:
you, so, don’t build one. The dev
- Page 3163 and 3164:
Where two of the L2 coils are shown
- Page 3165 and 3166:
As there are very slight difference
- Page 3167 and 3168:
This system was soon changed when v
- Page 3169 and 3170:
I suggest that the plastic pipe use
- Page 3171 and 3172:
The approximate number of turns bet
- Page 3173 and 3174:
These windings can be made on a PVC
- Page 3175 and 3176:
We add in an earth ground, a capaci
- Page 3177 and 3178:
At this point, the pumping scheme w
- Page 3179 and 3180:
The ground wire carries the negativ
- Page 3181 and 3182:
The big question is, of course, wha
- Page 3183 and 3184:
always less powerful than the forwa
- Page 3185 and 3186:
Isolation transformer. The isolatio
- Page 3187 and 3188:
In principle, you can use the CISC
- Page 3189 and 3190:
Gentlemen! Make it and test it. A -
- Page 3191 and 3192:
As with most systems, the practical
- Page 3193 and 3194:
which you will note has repeating p
- Page 3195 and 3196:
that the current flowing through th
- Page 3197 and 3198:
Fig.3A illustrates a control circui
- Page 3199 and 3200:
its rate of depletion. It is not su
- Page 3201 and 3202:
to a test using a switching device
- Page 3203 and 3204:
This is to test the efficiency of t
- Page 3205 and 3206:
thousand pulses per second ("1 kHz"
- Page 3207 and 3208:
All of the Ainslie circuits mention
- Page 3209 and 3210:
The view above is of the underside
- Page 3211 and 3212:
Scientific Papers The following lin
- Page 3213:
http://www.free-energy-info.tuks.nl
Inappropriate
Loading...
Inappropriate
You have already flagged this document.
Thank you, for helping us keep this platform clean.
The editors will have a look at it as soon as possible.
Mail this publication
Loading...
Embed
Loading...
Delete template?
Are you sure you want to delete your template?
DOWNLOAD ePAPER
This ePaper is currently not available for download.
You can find similar magazines on this topic below under ‘Recommendations’.